- A Brief History of the Kanban Method
- What is Kanban?
- Types of Kanban Systems
- Kanban Workflow Structure
- Other Visual Tools
- Benefits of a Structured Kanban Workflow
- Kanban System Rules
- Just-in-Time Manufacturing and Kanban
- Understanding Kanban and Lean Manufacturing
- Using Kanban to Eliminate Waste
- SCRUM vs. Kanban: Agile Project Management Approaches
- What is Kanban Training?
- Implementing a Kanban System
Imagine overseeing a facility that only stocked just enough supplies to satisfy customer demand. There wouldn’t be excessive amounts of inventory or the need to halt production because a certain component was out of stock.
Utilizing a Kanban system makes this goal possible.
The Kanban approach diverges from older forecasting production methods and instead allows real time demand to trigger resupply. Making use of Kanban means companies won’t have to run the risk of wasting money by having too much inventory, which also means there will be inherently less quality assurance issues such as defects becoming hidden in stored products.
At its core, the Kanban approach reduces overproduction and eliminates downtime between production process steps.
Learn how to change a manufacturing operation from a wasteful push system to a lean pull system using the Kanban method.
A Brief History of the Kanban Method

Kanban was first used in manufacturing environments by Taiichi Ohno of the Toyota Motor Company in the mid-20th century. Beginning with American supermarket stocking techniques that caught Ohno’s attention, he noticed the supermarkets were able to function without storing excessive amounts of inventory.
Since many of the products grocery stores sell must be bought and consumed before the product is allowed to spoil or meet the expiration date, only storing the amount of food customers will buy is essential. To achieve this, supermarkets function by using real time demand—when customers purchase an item, the store restocks the shelf, then more products are reordered to replace what was bought.
In this approach, customer demand controls the movement and ordering of more product. Based off what Ohno learned, he went ahead and applied this idea to a manufacturing environment by developing a method to use visual cues to signal all parts of the manufacturing process at a select few of Toyota’s facilities.
What is Kanban?
Kanban is a Japanese word meaning signboard, sign, or card. A Kanban system primarily uses visual cues to signal when a particular work action should occur. In a manufacturing environment, for example, a card listing specific information can be sent from the shipping department to the assembly line requesting a certain number of products from the team. The Kanban card in this example serves as a link and visual signal between the two department teams and works to trigger the action of moving that material, enabling the work to occur exactly when it should during the project.
Busy, professional workplaces must have an easy time communicating between departments, individual employees, customers, teams, and suppliers about managing the movement of materials, parts, finished product, and other relevant process information across the network.
Examples of Kanban can also be seen to exist in the home. A person might have an organized pantry where they keep canned goods that don't spoil quickly. In this pantry, there are two cans of each food, one in front of the other. When a can is used, the second can is moved forward. This action—removing the first can from the shelf and moving the other forward—is the cue used to signal the need to buy more of that product, in which then it's added to the weekly shopping list.
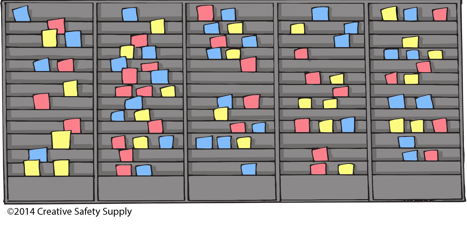
Systems based on the idea of Kanban are commonly used in hospitals, offices, homes, university services, warehouses, and countless more facilities. Used as a part of a Lean manufacturing system, many businesses have found Kanban as a beneficial way to reduce inventory and eliminate waste from the workflow.
Businesses that employ Kanban systems do so with specific rules in mind and meticulous planning before beginning the transition to this simple yet effective method for workflow management. No matter how different the unique
Kanban systems look from business to business, they're all based on the same basic idea: using visual cues to trigger team action.
Kanban Tools and Principles
Companies that utilize a project management system such as Kanban for their workflow can reap benefits such as:
- A higher ability to focus on continuous delivery—the creation of value
- Increased efficiency
- Increased productivity
- A higher rate of flexibility
- A reduction in wasted time and work
Gaining all those benefits of Kanban doesn’t come without a bit of work. That said, this agile project management system promotes six core practices and principles that help to maximize the portfolio benefits that a Kanban system allows its users. These Kanban method core principles include:
- Using a physical board or software to visualize the current workflow
- Limiting the number of WIP items being made to enable employees’ abilities to work rapidly
- Observing work to resolve bottlenecks and improve workflow
- Defining and share process policies
- Creating feedback loops to maximize efficiency
- Always striving for improvement by being innovative and prioritizing communication and collaboration
There are several kinds of tools that can be used to achieve the goal of implementing a Kanban system with your work management team. These work items include software options that allow the users to visualize the workflow and a more physical approach such as using Kanban cards, Kanban Bins, and Kanban Boards.
Types of Kanban Systems
There is not just one type of Kanban system that works for all organizations. Kanban must be tailored to each workplace to see the best results. There are six common Kanban systems that businesses can choose to implement for their project and production management. These Kanban workflow processes include:
- Production Kanban is the first and most basic type of Kanban system that can be implemented. It focuses on a list of items that need to be completed at specific times to maximize production flow.
- Withdrawal Kanban focuses on the movement of materials. Once one section of the process is completed by a team of workers, the part moves to the next stage.
- Supplier Kanban cards enable the suppliers of the current manufacturing process to be included within their supply chain network. Once work items run low, the users can send a request to the suppliers for more, streamlining distribution.
- Emergency Kanban cards are used when something requires immediate attention. This may be anything from replacing a defective part or suddenly needing more materials due to an increase in demand.
- Express Kanban cards deal with the shortage of an item and the immediate need for replacement. These are like emergency Kanban cards, but they don’t deal with defects.
- Through Kanban is a combination of both the product and withdrawal cards used by two production teams. Rather than having two separate cards, it is condensed to one that lets one team know that they need to start a task and move the finished material to the next stage.
Kanban Cards
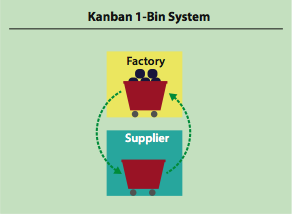
These cards are the main source of visual communication within the agile project management system that is Kanban. There are 1-card, and 2-card strategies that companies can use to maximize workflow productivity.
The information that Kanban cards may contain include:
- The name and part number of the item
- A description of the item
- The quantity needed
- The location of its use
- Supplier information
- Number in series (e.g., card 1 of 4)
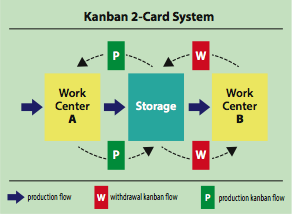
A 2-card system usually has three main locations and two loops rather than a 1-card system that is usually just used in the manufacturing facility. The 2-card strategy is one where if the shipping department needs products, it sends its Kanban card to the store. The store provides the products and sends its Kanban card to the production line. The production line then begins making more products. The seamless nature of the method is what makes the Kanban process so effective.
Kanban Bins
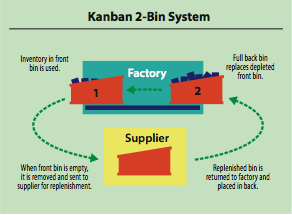
A 2-bin system is commonly used in storage areas at many types of workplaces. This approach can be used in warehouses, supply rooms at hospitals, places where ingredients are stored in restaurants or bakeries, and more.
This method functions by having two bins of a particular item placed one in front of the other, often on shelves. When the first bin is empty, it is removed, and the second bin is pulled forward. Then one of two things can happen. Either the empty bin itself will be placed in a designated location for reordering or a Kanban card placed at the back of the bin that has reordering information is placed in a separate location with other cards that specify reordering needs. This method is simple, but it helps ensure supplies never run out.
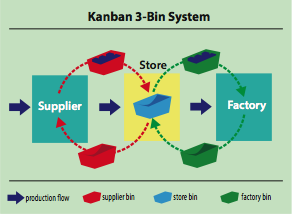
A 3-bin method connects different departments or different parts of work processes. In some cases, it even connects a company to its outside suppliers.
As an example, a basic 3-bin method functions by placing one bin at the factory where products are made, one at the store where parts/materials are held, and one at the supplier. When the factory runs out of parts, it sends its empty bin to the store to be refilled. The store fills the bin and now sends its own newly emptied bin to the supplier. The supplier team then sends a full bin to the store. The bins serve as the signal that each downstream part of the process needs more of something. They also give permission to move those things; in Kanban, nothing moves without permission.
Most 3-bin systems also keep Kanban cards in the bins specifying what the bin contains and at what quantity. Conveying the appropriate information is important since one of these bins is leaving the site to be refilled by another company. Getting the right data passed on is key to the success of the Kanban process.
Electronic Systems
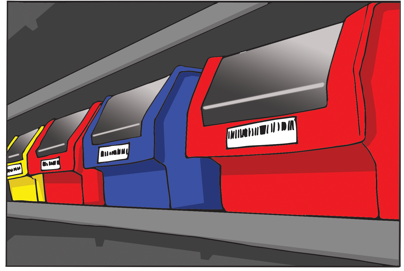
Advances in technology have allowed many workplaces to transition away from physical cards and bins. In electronic Kanban systems, barcodes are placed on items, on materials, or in specific locations. These barcodes are scanned when more of something is needed for the workflow, which sends a signal to the correct person or department to fill the request. Some systems even generate emails when certain barcodes are scanned that send orders to external suppliers and services.
Kanban Workflow Structure
The Kanban workflow structure is a visual representation of the stages tasks progress through within a project. It utilizes a Kanban board, which consists of columns and cards. Columns represent the different workflow stages, while cards represent individual tasks or work items.
Core Elements:
- Columns: These represent the distinct stages a task goes through, from initiation to completion. The most basic Kanban workflow includes three core columns:
- To Do: This column holds tasks that are planned but haven't yet begun.
- In Progress: This column contains tasks that are currently being worked on.
- Done: This column holds completed tasks.
- Cards: Each card represents a specific task or work item. The card typically contains details about the task, such as:
- A short description
- Assigned team member(s)
- Due date (optional)
Customization:
The beauty of Kanban lies in its flexibility. Teams can customize the workflow structure to reflect their specific needs. Here's how:
- Adding Columns: Depending on the project complexity, additional columns can be introduced. Examples include:
- Code Review (for software developme nt)
- Waiting for Approval
- Testing
- WIP Limits (Work in Progress): To prevent bottlenecks and ensure smooth workflow, teams can set WIP limits for each "In Progress" column. This limits the number of tasks that can be actively worked on at a time.
- Swimlanes: For complex workflows with multiple teams or categories, swimlanes can be introduced. These are horizontal sections on the board that categorize work based on team, project, or priority.
Other Visual Tools
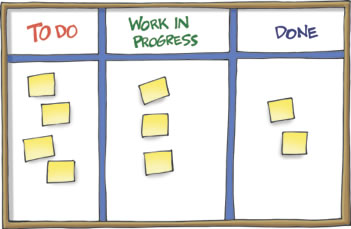
Kanban Board – A Kanban board makes it easy for people to see work in process. Basic boards might contain columns such as "To Do," "In Process," and "Done." A department might have a board that uses cards to represent all current work orders. Then teams can track the orders as they move through the workflow.
Kanban boards are often used in team settings outside of manufacturing to show which team is working on what.
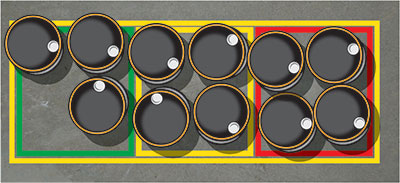
Floor or Shelf Markings – Some workplaces or storage areas choose to use color-coded floor or shelf markings to indicate when something needs to be produced or ordered. For example, a warehouse might store all the same item in the same area and then place red, yellow, and green floor marking tape on the floor that reveals itself when project inventory is getting too low.
When an item is at the green level, nothing needs to happen. At yellow, production might begin. At red, levels may have gotten too low, and steps need to be taken to quickly fix the problem. In this scenario, the colors themselves are the visual Kanban cues that trigger actions from the project management team.
Benefits of a Structured Kanban Workflow
A well-structured Kanban workflow offers a multitude of advantages for teams and projects. Here's a detailed breakdown of its key benefits:
- Enhanced Visibility: A Kanban board provides a clear and centralized view of the workflow stages and the current status of each task. All team members can easily see what tasks are upcoming (To Do), what work is actively being progressed on (In Progress), and what has been completed (Done). This transparency fosters better understanding of the overall project landscape and individual task dependencies.
- Improved Workflow Management: By visualizing the workflow, Kanban helps identify bottlenecks and inefficiencies in the process. When tasks pile up in a particular column, it indicates a potential bottleneck. Teams can then analyze the reasons behind the slowdown and take corrective actions to streamline the workflow. This continuous monitoring and improvement lead to a more efficient and optimized work process.
- Increased Team Focus: A core principle of Kanban is to limit the number of "Work in Progress" (WIP) tasks. This concept discourages multitasking and promotes focus on completing current tasks before taking on new ones. By focusing on a manageable number of tasks at a time, team members can deliver higher quality work and reduce the risk of errors.
- Improved Collaboration: The visual nature of the Kanban board fosters communication and collaboration within the team. Team members can easily see what each other is working on and identify potential areas for collaboration. The Kanban board also serves as a central platform for discussions and updates, promoting transparency and information sharing within the team.
Kanban System Rules
Kanban operates with a set of core principles rather than a strict set of rules. However, adhering to these core principles is crucial for successful Kanban implementation.
Here are the fundamental rules that govern a Kanban system:
- Visualize Workflow: The core principle of Kanban revolves around visualizing the workflow stages and tasks. This is achieved through the use of a Kanban board, which displays the different stages as columns and individual tasks as cards within those columns. This visual representation allows for easy identification of bottlenecks, task dependencies, and project progress.
- Limit Work in Progress (WIP): A key tenet of Kanban is to limit the number of tasks that can be actively worked on at any given time (WIP limit). This prevents multitasking and ensures focus on completing current tasks before taking on new ones. WIP limits are typically set for each workflow stage, ensuring smooth flow and preventing congestion.
- Manage Flow: Kanban emphasizes continuous flow of work through the system. Tasks should ideally move smoothly from one stage to the next without getting stuck. This is achieved by focusing on completing tasks efficiently and by identifying and addressing bottlenecks that hinder progress.
- Make Explicit Policies: While Kanban is flexible, it's important to establish clear policies for the system. These policies may include defining the workflow stages, setting WIP limits, and outlining the process for adding new tasks or prioritizing existing ones.
- Continuous Improvement: Kanban is an iterative methodology that encourages continuous improvement. Teams are expected to regularly review their workflow, identify areas for improvement, and adapt the Kanban system accordingly. This ongoing optimization ensures the system remains effective and aligned with the team's evolving needs.
Following these core rules establishes a strong foundation for a Kanban system. However, Kanban's flexibility allows teams to further customize the system to fit their specific project needs and team dynamics.
Just-in-Time Manufacturing and Kanban
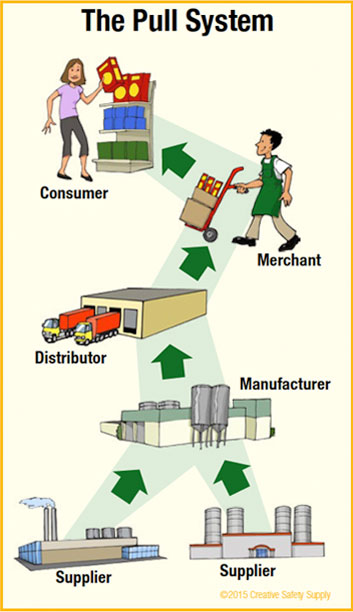
Because production is pulled through the workplace by customer demand, a Kanban system is often referred to as a pull system. A pull system is the opposite of a push system, which is the traditional way production has occurred in Western countries. A push system involves forecasting what demand will be based on historical data and current market conditions, and then scheduling production accordingly.
The downside of this method is that if demand changes quickly, a business could be left with a lot of products it doesn't need.
This system is called Just-in-Time (JIT) manufacturing because it is designed to produce the exact amount of a product needed at the time the customer wants it.
The benefits of this type of method are that it can reduce overproduction, eliminate waiting time between processes, reduce inventory of materials—which often are costly to store—and make it easier to respond to changes in demand.
Overall, a method that uses JIT manufacturing has built-in flexibility.
How does Kanban fit into this? Kanban cards, bins, or other visual cues are what control the JIT system. The Kanban cues are the mechanism that prompts the parts of the process to occur. JIT and Kanban go hand in hand, and they serve as the basis of what is often called the Toyota Production System.
Understanding Kanban and Lean Manufacturing
The production system practiced at Toyota has inspired many organizations around the world to change the way they do business and manage their workflow. In many Western countries, this system is referred to as Lean manufacturing, which aims to identify and eliminate wastes from work processes.
By eliminating waste, a business only spends time on things that add value for the customer.
Using Kanban to Eliminate Waste
Lean manufacturing tries to eliminate three main types of workflow waste, which are called the 3 M's: Muda, Mura, and Muri.
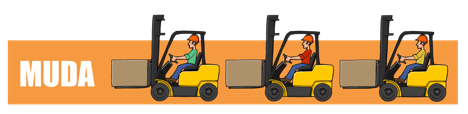

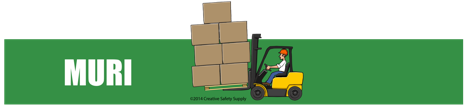
- Muda translates to “unnecessary effort” – As is the most basic type of waste, Muda is anything that doesn't add value to the end product.
Lean specifies eight main types of Muda:
- Over-production
- Unnecessary transportation
- Extra motion
- Waiting
- Over-processing
- Inventory
- Un-utilized talent
- Mura translates to “unevenness” – Mura refers to irregularity in the production process. This occurs when team members and materials aren't allocated appropriately. Mura often results in spikes in production and frequent stops and starts.
- Muri translates to “overburden” – While Mura might periodically overburden people and equipment, Muri is the consistent overburden of these assets. This overload can cause strain, injuries, defects, and breakdowns, and in the long run it will likely be unsustainable.
Overall, Kanban and JIT are important parts of a Lean manufacturing environment for many reasons, but because they can help eliminate many of these wastes. Kanban and JIT can make production more even, reduce inventory, and eliminate overproduction.
WIP Limits
When overproduction occurs, there are often too many of a particular part, material, or product in process at once. Having so much work in process can cover up problems with the process itself. On the other hand, with too little work, teams of employees often end up wasting time by waiting for a project to begin.
When set up properly, Kanban reduces the number of tasks occurring at the same time in a project and allows problems to surface. This can be made even easier if WIP limits are established.
Establishing WIP limits is one of the main ideas that Kanban emphasizes to correctly allocate resources and time to a smooth workflow. It also helps to increase the productivity of processes as it only allows employees to work on the tasks in front of them. As a final point, WIP limits allow team members to spot project bottlenecks in the process to then be able to fix them accordingly.
SCRUM vs. Kanban: Agile Project Management Approaches
SCRUM and Kanban, while both falling under the umbrella of Lean manufacturing strategies, are not identical. However, they can be effectively combined to create a robust kanban system for agile project management.
Here's a breakdown of some key differences between SCRUM and Kanban:
- SCRUM utilizes predefined roles. The SCRUM master manages timelines, the product owner communicates project goals, and the development team executes tasks. The kanban method, on the other hand, is more flexible with less rigid roles.
- SCRUM relies on sprints, fixed timeframes for completing specific software development tasks. In contrast, Kanban promotes continuous delivery throughout the workflow.
- Both methodologies utilize a pull system, but SCRUM works in batches, while Kanban focuses on individual steps.
- SCRUM discourages mid-project changes, whereas Kanban embraces fluidity to accommodate shifting priorities.
- SCRUM excels in situations with stable priorities. Kanban, however, is ideal for projects with frequent changes.
- SCRUM gauges success based on the completion of the latest sprint. Kanban, however, uses kanban cycle time to determine productivity.
The beauty lies in the potential synergy between Kanban and SCRUM. Because Kanban thrives on workflow visualization, it can seamlessly integrate with SCRUM at any point. This hybrid approach can empower your team to leverage the strengths of both methodologies for a more adaptable and efficient project management system.
What is Kanban Training?
Kanban training equips individuals and teams with the knowledge and skills necessary to implement and effectively utilize the Kanban methodology within their projects. Training programs typically cover the core principles, practices, and benefits of Kanban.
Kanban training can be beneficial for various audiences, including:
- Project Managers: Kanban training helps project managers understand how to implement Kanban for project planning, workflow management, and continuous improvement.
- Team Members: Team members gain an understanding of the Kanban system, their roles and responsibilities within the workflow, and how to collaborate effectively using Kanban boards.
- Leaders: Leaders can leverage Kanban training to understand how Kanban can enhance team productivity, improve project delivery, and cultivate a culture of continuous improvement within the organization.
Kanban training programs can be delivered in various formats, including online courses, workshops, and in-person training sessions. The specific content and duration of the training program can vary depending on the provider and the target audience.
Implementing a Kanban System
The examples of Kanban systems described thus far only use a few bins or cards, but in a large manufacturing process many more signals may be needed. Anyone implementing a Kanban system will need to determine how many cards and bins to have throughout the process, as these numbers determine how much of something will be on hand at once.
These calculations are based on considerations such as:
- Demand
- Lead time
- Downtime
- Changeover time
- Length of shift(s)
- Safety stock
Having more Kanban signals in a process means there will be more materials in the system, but this isn't necessarily a bad thing. Most Kanban systems need a certain amount of buffer materials to accommodate customer orders and ensure that development happens on time.
The scale of Kanban implementation must also be considered. Kanban works best when implemented across the whole organization rather than only in certain business processes. When Kanban is only used in certain areas, problems may develop between the parts of a business that use the pull system and those still using a push system for new product development.
Is Kanban the Answer?
While Kanban effectively reduces inventory and levels production for many businesses, decision makers will have to determine whether it suits their business, and if so, what type of Kanban system would work best.
Any organization thinking of using Kanban should assess the current state of processes, do some research and collect data, and potentially seek advice about the best solutions for their workflow.
That said, no two Kanban systems are the same, but they all have several important things in common:
- Kanban systems use visual signals to trigger actions. Nothing happens without a signal.
- Kanban systems can help prevent wastes such as excess inventory and overproduction.
- Kanban systems put control of the system into the hands of everyday workers, not just managers.
Actions are limited by Kanban, as is the quantity of work in process. By limiting these things, Kanban makes it easier to see what's going on in a work process. This way, problems involving waste will more easily surface and have the chance to be fixed.
Kanban will most likely require thinking about work processes in new ways. However, when businesses do decide to use Kanban, they often see many benefits in the long run. Processes begin to run more smoothly, and issues can be resolved quickly.
Similar Articles
- Floor marking comprehensive research, education and training
- Advanced Kanban: Optimizing Complex Systems
- Kanban Production System
- Implementing Kanban
- Implementing 5S | Tools and Training
- Kaizen and Lean Manufacturing
- What is Logistics Management? (Supply Chain)
- Heijunka (Production Leveling)
- 5S Lean Training
- Toyota Production System (TPS & Lean Manufacturing)