Tips To Maintain Fire Safety in the Workplace
Fire safety in the workplace is incredibly important no matter the industry since it can happen anywhere at any time. Each facility should adhere to established fire codes, perform a thorough assessment of present fire hazards, have an extensive understanding of fire suppression equipment, and have a comprehensive emergency plan in place.
In this blog, we’ll go over the potential workplace fire hazard examples and the specific fire prevention methods to help minimize the risks.
What is the golden rule of fire safety in the workplace?
In fire safety, the paramount principle is prevention. Practicing fire prevention at work minimizes the risk of a fire starting in the first place. This can involve a multitude of measures, such as maintaining electrical systems, eliminating flammable hazards, and implementing fire prevention practices in the workplace. By prioritizing fire prevention at work, workplaces can significantly reduce the likelihood of fires and safeguard both employees and property.
Examples of Fire Hazards in the Workplace
Let’s go over the examples of workplace fire hazards and the appropriate fire safety tips to implement in the workplace.

Electrical Equipment And Areas
Between 2011 and 2015, lighting and electrical distribution equipment were the leading cause of structure fires on industrial properties. Electrical issues, such as damaged extension cords, blocked electrical panels and heaters, and overloaded circuits often lead to fires. Fires are also commonly caused by electrical events such as arc flashes.
Fire Prevention At Electrical Workplaces
Maintenance of power cords and other electrical equipment should be conducted regularly. Organizations should regularly conduct electrical inspections to avoid malfunctions that result in bodily injury or increase the risk of fire hazards. During an electrical inspection, it’s important to have sparking outlets or faulty wiring addresses which is the main cause of electrical fires. Implementing basic workplace fire safety measures such as hiring a licensed electrician who can diagnose potential fire hazards before they occur.
Flammable Liquids And Gases:
Workplace fires are also commonly caused by improper storage of flammable material or a buildup of combustible dust. Flammable and combustible materials both burn, just at different flash points; the difference between being “flammable” and being “combustible” is that flammable materials have low flash points (low temperatures at which surface vapors will ignite), and combustible materials have high flash point. Both are dangerous and should be properly handled and stored to ensure fire prevention in the workplace.
Flammable Substance Fire Prevention At Work:
The first step of workplace fire safety is to develop a system of proper handling and storing of flammable materials in well-ventilated areas away from potential heat sources. Your employees should be educated on the rules of proper conduct to safely handle such materials to further contribute to workplace fire safety practices.
Faulty Heating Equipment
Workplaces with heating equipment like furnaces, space heaters, and boilers are at higher risk of fires if not properly maintained. It’s necessary to ensure workplace fire safety measures are implemented in such workplaces for maximum protection.
Fire Prevention Measures:
For factories or workplaces with heating equipment, scheduling regular inspections and maintenance for heating systems helps mitigate the possibility of a fire hazard. The fire safety presentation workplace practices aid in developing a safety culture.
OSHA recommends a comprehensive hazard assessment of all materials, operations, spaces, and potential ignition sources within a facility to reduce the risk of these dangerous events.
Best Workplace Fire Safety Tips
There are several fire prevention safety practices to keep your employees and business safe from potential fire threats at work, like employee fire training and providing protective equipment.
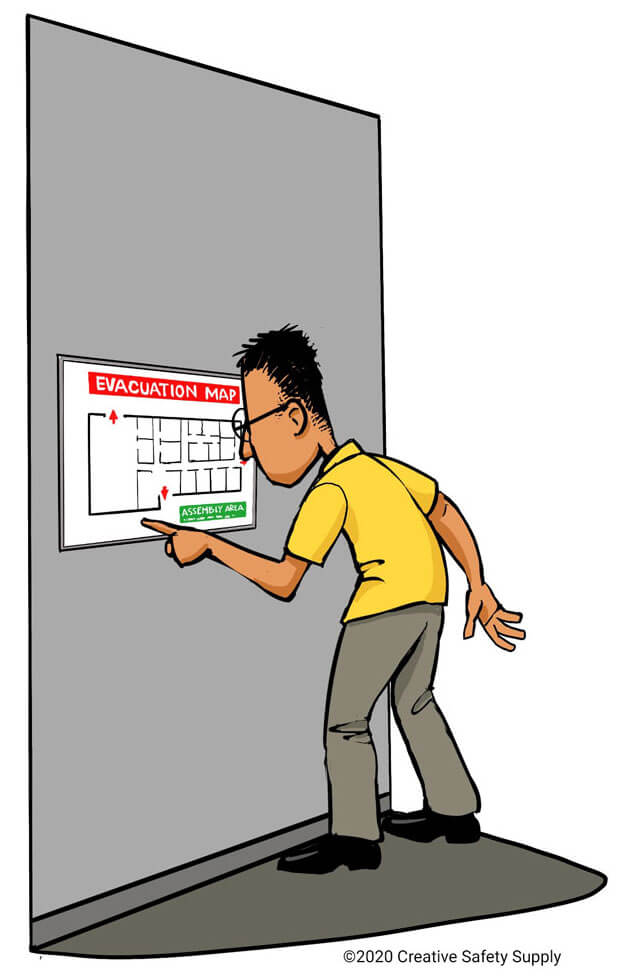
Employee Training for Fire Safety
If a fire breaks out in your facility, employees rely on their training to ensure their safety. While certain occupations, such as welders and electricians, require high levels of fire safety training, every employee in any occupation should be trained on general fire prevention and safety strategies so they understand how to keep their area—and themselves—safe. OSHA 1910.39 establishes general training requirements that each employee should receive, which cover:
- An understanding of the examples of fire hazards and potential ignition sources within their vicinity. This is often the first step in a fire safety program.
- Emergency exits. Training should cover the locations of the exits, how to identify them, and which ones are nearest to an employee’s typical location.
- Fire drills. These should be conducted regularly so workers can practice what to do and where do go in the event of a fire.
- Fire extinguishers. If extinguishers are provided for employee use, the employer must implement training so workers are familiar with the principles of the extinguisher and how to use it. This training should be conducted when the worker is first hired, as well as once a year, and needs to include what type of fire extinguisher should be used based on the materials in the area.
Additional fire safety training may be necessary depending on the risks and operations associated with the facility. The employer is responsible for identifying these additional needs and providing appropriate training. Extensive preparation and a basic understanding of fire safety for each worker in your facility is critical to avoiding fires in the first place, and to ensuring that both lives and property are saved if one does break out.
PPE for Fire Safety
Firefighters are required to wear extensive personal protective equipment. Most workers don’t need this type of PPE during day-to-day operations, However, there is fire safety PPE available for people who consistently work in situations where there is an increased risk of a fire breaking out. There is flame-resistant clothing for workers who work with flammable liquids or chemicals, in kitchens, in welding, or with saws and other types of equipment that may set off sparks.
Providing your employees with such fire safety equipment can help them make effective decisions during the initial breakout stages. Taking effective fire safety measures helps reduce the risk of a fire which may incur high property damage.
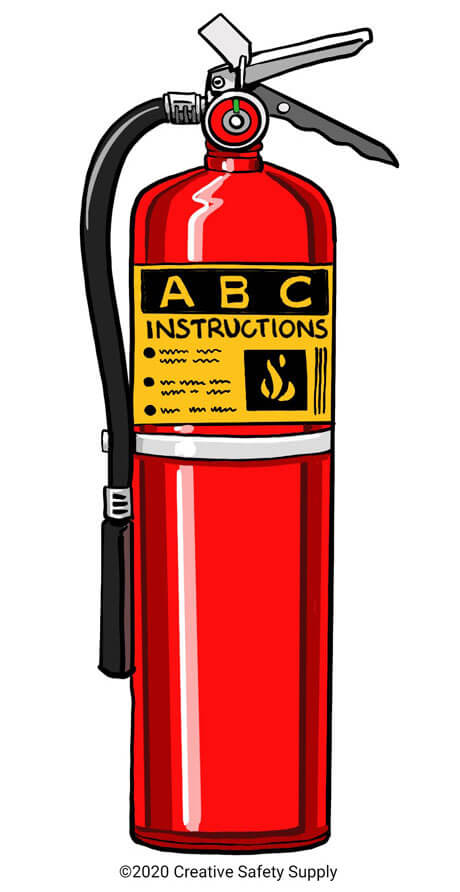
Fire Safety Regulations and Standards
In the United States, there are three main organizations involved in fire safety regulations. These are the IFC (International Fire Code), OSHA, and NFPA.
The NFPA is the leading resource for fire hazards and safety. There are several NFPA codes regarding the workplace that are particularly important:
- NFPA 30: Flammable Liquids Code, which focuses on the safe storage of flammable liquids. Safety labels included with these liquids should list their name, flammable warning, flash point, and fire point.
- NFPA 70: National Electrical Code (NEC). This code is essential for electrical professionals, as it establishes procedures for the safe installation of electrical wiring equipment.
- NFPA 70E: Standard for Electrical Safety in the Workplace. A cousin to the NEC, this code applies to every business. It specifically focuses on three kinds of energy hazards: arc flash, electrocution, and arc blast. These hazards often cause fires.
- NFPA 72: National Fire Alarm and Signaling Code. This provides standards on fire detection and emergency communications and also covers mass notification systems for public threats such as nuclear, biological, and chemical emergencies.
- NFPA 99: Fire Safety in Healthcare Facilities, a specialized code that was adopted to address the unique environment and hazards of healthcare. In 2012, NFPA 99 became a code instead of a standard and adopted a risk-based approach.
- NFPA 704: Standard System for the Identification of the Hazards of Materials for Emergency Response, which provides a consistent labeling system for communicating hazardous materials to first responders. This code is well known for standardizing the fire diamond, which is divided into four color-coded sections and covers flammability, instability, health hazards, and special precautions.
Established by the International Code Council, the International Fire Code (IFC) is a document recognized around the world that standardizes fire safety and establishes requirements for fire protection systems, as well as fire prevention plans. It is currently used in 40 states and was created with the intention of worldwide application.
One of OSHA's primary areas of focus is fire prevention in the workplace. OSHA's standard 1910.39, “Fire Prevention Plans,” establishes requirements that help employers reduce the risk of fire and ensure that employees will be safe if a fire does occur. The standard covers requirements for a prevention plan, emergency exits, employee training, fire suppression options, and the identification of flammable or combustible materials and ignition sources. If your workplace has ten or more employees, you are required to have a fire prevention plan.
Similar Articles
- Fire Prevention in the Workplace [OSHA 1910.39]
- NFPA 25: Standards for Fire Protection Systems
- Addressing Biohazard Safety in the Workplace
- Improving Workplace Electrical Safety
- Fall Protection in the Workplace: OSHA’s Guidelines
- Floor Marking for Fire Extinguishers
- Mine Safety & Health [Expert Advice]
- Job Hazard Analysis: Addressing Coronavirus Risk in Your Workplace
- Preparing the Workplace with Emergency Action Plans (EAP)
- Workplace Safety Inspections & Audits