FOCUS-PDCA is a business strategy designed to improve processes. The name is an acronym that describes all the different steps and actions that need to take place during the process improvement period. This improvement strategy can be used in any type of industry, but it was originally developed for the healthcare industry by the Hospital Corporation of America (HCA).
What Does FOCUS Stand For?
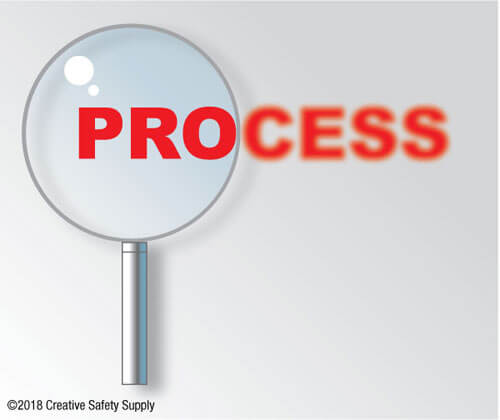
- Find a Process to Improve - This is the first step of the strategy and involves someone identifying a process that needs improvement. Sometimes the process may need a major improvement due to serious issues, but just as often the process already works well but still has room for improvement.
- Organize an Effort to Work on Improvement - In this step, a team of people who are familiar with the problem is gathered together. In most cases, the team is made up of people from a variety of areas involved with the process being improved. This helps ensure the improvement incorporates input from all sides of the issue.
- Clarify Current Knowledge of the Process - Once the team gathers together, all the knowledge they have about the process is presented. Questions should be asked and answers given to clarify what each member of the team means. This will ensure everyone is on the same page regarding what the problem is and what the proposed solution will be.
- Understand Process Variation and Capability - One of the most common causes of problems in a process is the variations that exist. All processes have some variation, even if it is minor. Looking at the processes closely and discussing them in depth will help identify the right strategy.
- Select a Strategy for Continued Improvement - In this stage, an improvement plan is selected to test. The team should choose the solution to the problem that they feel will provide the best results. Part of the improvement plan should be a list of expected results so that once tested, the results can be measured to determine whether or not the strategy was successful.
What Does PDCA Stand For?
Once the FOCUS steps have been completed, it is time to do a test implementation of the selected strategy. This is where the PDCA process is used. PDCA is another acronym, which stands for:
- Plan - Creating an action plan for the implementation process is critical. This plan should include a list of required steps, detailed assignments for each person on the team, a timeline for completion, and goals to hold people accountable.
- Do - This is when the plan is implemented. Complete the steps from the planning phase in the proper order and follow the strategy properly. If this stage is not done properly, it will produce invalid results that make it impossible to know whether the original process improvement strategy worked.
- Check - Once the plan has been implemented, the team takes measurements to determine whether they are getting the desired results.
- Act - Based on the results of the check stage, the team either confirms that the process improvement idea was a success and turns it into a policy or finds that it had problems and comes up with solutions. If the improvement process didn't go as planned, the team must start over with the PDCA cycle.
Sources
- https://www.isixsigma.com/plan-do-check-act/resource-page-plan-do-check-act-or-pdca/
- https://asq.org/quality-resources/pdca-cycle
Similar Articles
- An In-Depth History of the Kaizen PDCA Cycle
- Organizational Development Process
- What is a Kaizen Event? [Planning and Execution]
- 8D for Problem Solving
- Hoshin Kanri
- Getting Started with Kaizen
- Continuous Improvement (A Kaizen Model)
- Workplace Safety Inspections & Audits
- Kaizen (Lean Continuous Improvement)
- Understanding the SIPOC Diagram in Six Sigma