The implementation of lean management methodology to ensure supply chain performance is defined as lean logistics. The principle of lean logistics is to analyze and eliminate operations which do not contribute to ensuring the flow of goods and services in a smooth manner to save expenses.
Applying lean logistics to the supply chain consists of doing more with less effort, less equipment, less cost and less time. These set of methods were developed by Taiichi Ohno at Toyota, within the industrial production field, hence it is referred to as lean manufacturing
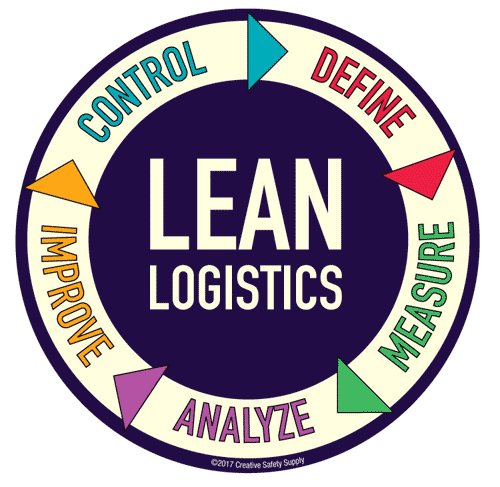
Principles of Lean Logistics Methodology
When implementing lean logistics, it is important to understand the lean principles that will help guide a company through the process. These principals will need to be understood and followed at every stage of manufacturing in order to eliminate waste and run efficiently:
-
Determine Value - Knowing what customers want will help to determine what is valuable. If customers won't pay for it, it does not have value.
-
Eliminate Waste, Boost Efficiency - Breaking down the manufacturing process into individual steps is an important part of identifying waste and eliminating it. It can also be helpful in taking steps to improve the production process.
-
Improve Process Flow - Improving flow helps to ensure things are done in the right order, at the right time, and in the right way. By organizing the process flow properly, lean can offer many benefits to any environment.
-
Use Pull Strategies - Rather than creating products and hoping that customers will buy them, allow customers to pull the products as they are needed. This reduces waste and risk in production.
-
Monitor and Maintain Change - Always be looking for ways that the process can be improved. This can be through improved machinery, improved policies, or any number of things. Constantly striving for perfection is an important part of lean logistics.
These principles will help a company to not only properly implement lean logistics, but also to keep using it long into the future to get continuous improvements.
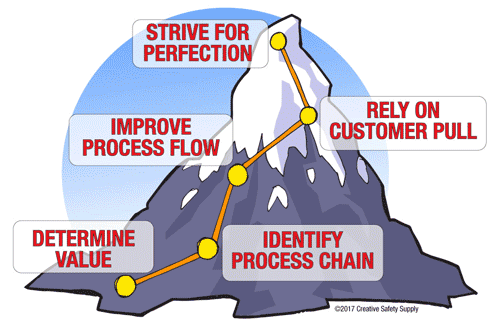
Importance of Lean Logistics
Lean logistics should be looked at as a long-term investment into improving quality, reducing waste, and benefiting the bottom line for a company. Some efforts will yield immediate results, but many others may take years before the benefits are fully realized. By continuously evaluating how things are done throughout the process in question, and identifying ways to make improvements, a company can find many ways to create a workplace that is safer, more efficient, and better for everyone involved.
Where Can Lean Logistics be Used
Lean logistics can help reduce or eliminate waste in just about any environment imaginable. The concepts are broad enough to be able to be modified or adapted to fit all sorts of industries. The following are some of the different types of companies that take advantage of lean logistics.
- Manufacturing - The manufacturing industry is where lean got its start. This is still, by far, the most popular industry where lean strategies are used.
- Office Jobs - Office environments can benefit greatly from lean methodologies. There are many informational resources on how to implement lean into almost any office environment.
- Auto Mechanics - Auto mechanics and garages often have a significant amount of waste, which can make them quite inefficient. Harnessing lean logistics can cut down on waste significantly.
- Product Design - This is one industry that many people overlook when it comes to lean concepts, but it too can benefit from smart processes.
- Hospitals - Hospitals are adopting lean logistics at a very fast rate because reducing mistakes can help save lives. In addition, one of the ways to reduce waste is to keep things clean, which is of utmost importance in a hospital.
Each of these types of work has proven examples of how lean can benefit them. When companies are looking to begin using lean logistics, they can turn to existing examples of where it has been beneficial and learn from them to help make the implementation easier.
Benefits of Lean Logistics:
One of the main benefits of lean logistics is inventory management. Additional excessive inventory leads to waste and minimal inventory results in more wait time leading to unsatisfied customers. By practicing lean logistics into your business, you can achieve:
- Team Management
- Efficient Business Processes
- Better Management with No Set Backs
- No BottleNecks
- Reduced Costs
- Enhanced Productivity
By practicing lean logistics into your business operations, you can learn to reduce costs and manage manufacturing of goods and products effectively without suffering any kinds of losses.
Similar Articles
- What is Logistics Management? (Supply Chain)
- 5 Lean Principles for Process Improvement
- What is Toyota Lean Management?
- 8 Wastes of Lean [A Guide to Manufacturing Wastes]
- Applying Lean Principles in Healthcare
- Lean versus Six Sigma: Which is better for your business?
- What is Lean in Business?
- Lean Thinking: The Foundation Of Lean Practice
- Kaizen and Lean Manufacturing
- House of Lean