Jinshuken is a kaizen strategy which means “self-study” in Japanese. It focuses on intentional, self-learning and the practical approach to improving existing procedures by visiting the actual site of the process. For instance, floor managers practicing Jinshuken would have to visit the production site and observe existing procedures in their natural state to make changes.
The origin of Jinshuken comes from “Kanban houshiki bukachou jishu kenkyuukai” which translates to “Kanban system department and section manager autonomous study groups.” For convenience, it has been shortened to “self-study” but is commonly called “autonomous study groups,” in workplaces.
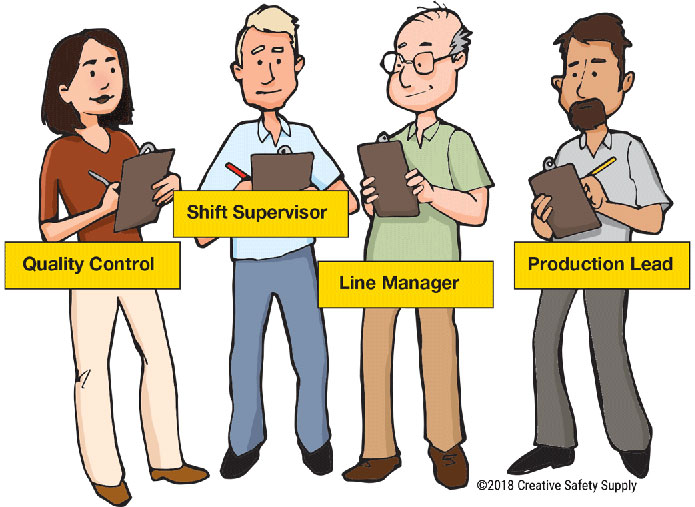
What Is The History Of Jinshuken?
The concept of Jinshuken originated from Kanban, which is a visual card to ensure smooth workflow and is generally applied as an “autonomous self-study group” for kaizen (self-improvement) in organizations. This culture of “continuous self-improvement” began with the Toyota Production System, where concepts such as kaizen, jinshuken, and Gemba were developed.
Taiichi Ohno, the owner of the Toyota Production System and the mastermind behind kaizen implemented jinshuken by gathering managers on the factory floor to practice hands-on kaizen activities. This activity of self-learning would involve department managers and section managers from the Motomachi and the Kamigo factories gathering together, choosing a “theme” or a set of problems, and devising solutions to improve natural processes.
This practical approach of kaizen, allowed the managers to assess naturally occurring processes within the supply chain and build a culture of Gemba or genchi genbutsu which means, visiting the actual site to improve processes.
Jinshuken can be a day-one activity in a kaizen workshop within organizations. Toyota’s Operations Management Consulting Division implemented this process of “self-learning” to develop skills and increase the participation of floor or division managers to reduce bottlenecks or eliminate waste. This system of kaizen in Toyota Production Systems was normally observed in supplier operation projects which lasted from three to four months, to reduce lead time and focus on perfection. The primary objective of Jinshuken is to provide solutions and produce a culture of continuous improvement where a set of linked operations takes place.
The strategy behind jishuken is primarily aimed at getting team leaders and managers to conduct hands-on kaizen activities in the operational area, like the factory floor where there is a large margin of error.
Jinshuken Implementation: Getting the Leadership Involved
One of the biggest benefits of Jishuken is that it is primarily focused on the activities of the facilities leadership teams. This includes everyone from the manager level all the way up to the CEO. In many companies that use Kaizen strategies, most of the real work is done by the front-line employees and entry level supervisors.
The management teams simply endorse the efforts and ensure that any necessary budget is there, and that all teams are putting in good effort toward continue improvement initiatives. The idea that CEOs and other top-level management teams are 'too busy' or 'too important' to get involved with this type of work has been very pervasive, which can cause problems.
Without direct high-level management involvement in continuous improvement programs, many problems can be introduced. It can even get to the point where upper level management really has no idea how things are done in their company, which can prevent them from being effective leaders. Bringing these managers down onto the shop floor, and helping to ensure they have a strong operational understanding of how things work can yield many important benefits.
Practicing Kaizen In Toyota Production System
Toyota Production System implements Kaizen through the following steps in their Jishuken processes:
Area for Improvement:
Managers need to identify a specific area where improvement is needed.
Team:
A team will be developed to address the area of improvement. This team will include a leader as well as individuals from different departments who will be affected by any changes. Members from quality control and other systems should also be included.
Monitoring Functions:
Each member of the team will given specific monitoring functions that they will be responsible for.
Questions:
Team members will need to ask questions about different tasks related to the area where improvement is needed. This step is used to gather as much information about the area as possible before making any changes.
Jishuken Worksheet:
The leader of the team will have a worksheet that tracks any issues, as well as countermeasures or solutions for those issues. This sheet should also identify who would make the listed changes.
Meetings:
The team leader will meet with the various operators in the areas where changes are to be made to discuss potential changes to be implemented.
Posting:
All results will need to be posted in an area where they can be seen and reviewed by all members of the team, and any impacted areas.
The Difference: Jinshuken VS Kaizen
While Jishuken and Kaizen are closely related, they are not the same thing, and confusing the two needs to be avoided. One of the simplest, yet most important, differences is that Kaizen is a cultural or philosophical effort, whereas Jishuken is the intentional, workplace activity to practice Gemba (go and see) in an organization.
Generally, Kaizen activities are initiated to improve existing or known bottlenecks within the organization. In comparison, Jinshuken is targeted to explore Transaction Processes Systems within an operation to introduce improvement. Jishuken should have very specific tasks and activities associated with it. The point of these tasks is to solve a specific problem. The problem will be solved using Kaizen principles and will help to further develop and foster the Kaizen strategies in the workplace.
How To Design A Jinshuken Workshop?
You can introduce Kaizen into your organization by creating a Jinshuken workshop by:
Creating a Team
When using Jishuken to solve a problem, the creation of the team will be one of the most important steps. While each company can make its own standards, one team will usually be made up of 5-7 different team members. These members will all be managers or above, and they will work together to identify solutions.
Team members can, and should, consult with their employees and other members when gathering the information they need. Those who are actually on the Jishuken team, however, will be part of the overall leadership team. All members of the leadership team within a company should be involved with Jishuken at certain times.
Focusing On Improvement
Jishuken will help to identify specific problems that need to be solved within the workplace. These issues will then have the focus of the leadership team, and they can come up with effective solutions. Management will naturally have the buy in of their teams, which can make it easier to find solutions. It is important for management to really analyze issues, and talk to the people who are affected, to get an in-depth understanding of how their changes will affect the area.
Only Necessary Changes
Managers can sometimes get drawn into the strategy of 'change for the sake of change.' This is when the managers know that continuous improvement is the goal, so they look for almost any situation where change is possible and treat it like a problem to be solved. Members of a Jishuken team need to always keep in mind that the only changes that should be made are those that are justified by the existence of a problem.
The changes should also have a very significant ability to solve the problem that has been found. Making significant changes and hoping that they will fix the issues at hand will cause employees to become distrustful of this process, and it can also cause additional problems to be created.
Effective Jishuken Training
One obstacle for many companies when it comes to implementing Jishuken is the training that is needed. Getting all the managers to attend the training that will be necessary to get a strong understanding of what Jishuken is, and their required involvement, can be a challenge in some environments.
Without proper training, the Jishuken activities will not be nearly as effective as they could be, and in some cases could even be detrimental. Many companies will bring all the managers to an offsite training seminar or retreat-style event to get them all up to seeped. Jishuken strategies aren't extremely complex, however, so it won't take an extended period of time to ensure everyone is able to participate in the Jishuken strategies.
FAQ’s:
What is the difference between Kaizen and Jinshuken?
While the motive behind both concepts is to introduce improvement, kaizen generally means to observe areas of improvement, and Managers are asked to devise strategies to resolve them. In contrast, Jinshuken means to “self-learn” meaning that Managers are asked to choose an area and practice self-learning to learn how operations work. This promotes Gemba and ensures the involvement of multiple sectors together.
What Is Jinshuken In Toyota?
Jinshuken revolves around kaizen, which is the core of continuous improvement. In the Toyota Production System, managers from different floors are gathered together on the factory floor or where operations are conducted to practice kaizen activities. During a Jinshuken workshop, areas where changes can be made to ensure deadlines align with company business targets.
What Is The Jinshuken Approach?
Jinshuken is a sublet from the Kaizen culture of continuous improvement. While it originated from Kanban, it has its own practical approach to addressing problems from the lowest level, (where productions are operated) and promotes interaction between various departments such as production, operations, maintenance workers, and management. Jinshuken is designed to assist managers to better understand how kaizen works and implement it to ensure smooth operations.
What does Jinshuken mean In Japanese?
Jinshuken literally means “self-learning” in Japanese and is generally used to refer to “autonomous self-study groups”. This includes the interaction of Managers to “Self-learn” how operations work and choose their learning process to improve existing operations along the value chain.