Now that clutter has been eliminated with Sort, and the space has been organized with Set in Order, it’s time to sanitize with Seiso, or the Shine phase. During this step, the entire workstation should be completely and meticulously cleaned. Shining the workspace is critical for sustaining the improvements made during the first two phases of 5S. Every area in the workspace must be addressed when cleaning, this includes storage areas, machines, equipment, tools, and work surfaces.
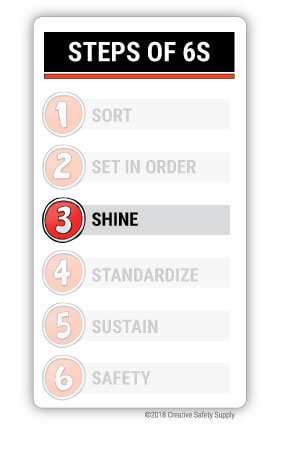
Once the area has been thoroughly cleaned, it must be maintained. The Shine phase is not a one-time task, but rather a task that should be completed on a day-to-day basis. Although the janitorial staff usually completes all cleaning jobs, the detailed cleaning of this step should be done by employees. At the end of each day workers should return tools and materials to their homes and clean up their spaces before leaving.
Why the Shine Step is Important
Because workers are cleaning daily, it is an ideal time to complete inspections and regular maintenance on machines. When a piece of equipment or machinery is kept clean, employees can easily spot malfunctions that need to be fixed. When these issues are identified and addressed early on, a facility will most likely avoid equipment failure and loss of production.
Following the implementation of this phase, some noticeable changes may take place in the facility. First, employees are more likely to be invested in their work because this responsibility inspires ownership of their space. Second, because the equipment and surroundings are kept in great shape, fewer injuries will occur and equipment breakdowns will be infrequent; that means greater productivity and fewer costs!
Cleaning may seem like straightforward process but having a standardized cleaning program can make all the difference. Employees should be trained on how to properly Shine their workspaces. They know what they need to clean, how to clean it, where the cleaning materials are stored, and how to identify any malfunctions.
Explore the pillars of 5S:
- And consider adding Safety with 6S.
Similar Glossary Terms
- 5S – Set in Order
- 5S – Standardize
- 5S – Sort
- 5S – Sustain
- 6S – Safety
- 5S
- 6S
- Total Productive Maintenance (TPM)
- RCM (Reliability Centered Maintenance)