When implementing a 5S program into their facility, some managers choose to include an additional pillar: Safety. When Safety is added to the mix, the 5S program them becomes 6S. Some argue safety is an ongoing process already supported by the 5S system, but the goal of adding the Safety phase is to focus eliminating risks in work processes.
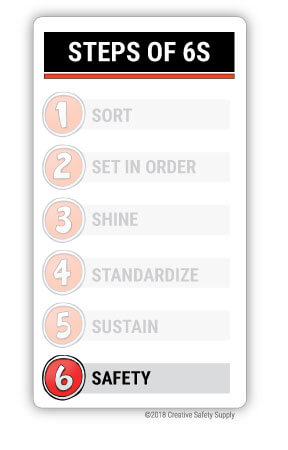
While the 6th S is not part of the original concept of 5S developed at Toyota, Lean experts all over the world have discovered that a facility’s safety program is just as integral to productivity and efficiency as any of the other 5S pillars. Since one of the guiding principles of all Lean methodologies is to eliminate waste, it makes perfect sense that safety issues that cause delays, damage, or worse, injuries to employees, would need to be eliminated. Safety issues cause delays in production and can cost companies a lot of money; the 6th S helps businesses stay safe so that employees stay protected and production continues uninterrupted.
5S & Safety
Some people may consider the 6th S to be unnecessary, but a safety step just naturally fits with the other steps of 5S: Arranging spaces in logical ways, organizing tools and materials, and cleaning regularly makes it easier for people to do their jobs without tripping, slipping, experiencing an ergonomic injury, etc. Therefore, Safety has established itself as the 6th S, and its benefits is worth re-evaluating safety at your facility.
The 6th S also helps facilities stay in compliance with OSHA regulations and other standards, so this is a step not to be skipped. Companies that don’t follow safety standards, properly mark hazards, or fail to submit accident reports in a timely manner can receive costly penalties from OSHA. Strong safety programs can prevent all of that from happening.