The Risk Priority Number is a measure that’s utilized when assessing risk in the workplace. It helps to identify critical methods within your business’s process of design. Values range from 1, indicating the best, to 1,000, indicating the worst. Although the RPN is most commonly used in the automobile industry and aerospace, it may also be applied to a manufacturing setting.
A Risk Priority Number aids ongoing improvement and ensures the manufacturing process is as successful and secure as possible. RPN is commonly used in Lean Manufacturing. It's established by the Failure Modes and Effects Analysis (FEMA), a risk assessment tool. FEMA evaluates the detection, severity, and occurrence of risks and prioritizes them based on urgency. Those cases that are most common and severe should be addressed as soon as possible.
Severity, occurrence, and detection are each rated on a scale from one to ten, then multiplied together to provide the RPN. They are defined as follows:
- Severity (S) is a numerical estimate of how severe the risk is and how its effect will be perceived by either the customer or the end user. A one indicates a low risk of relevant effect, while a ten indicates that the risk is considered catastrophic and may result in highly unsafe operation, a defective product, or even death. Examples of severity ratings include:
- 10 (Hazardous); affects safe vehicle operation or involves noncompliance with government regulation
- 6 (Moderate); item/vehicle operable, but comfort and convenience are compromised and the user will experience discomfort
- 2 (Very Minor); fit and finish/squeak and rattle item does not conform, and the defect will be noticed by discriminating customers
- Occurrence (O) is an estimation that considers documentation of similar processes, analysis, and calculations. This is also known as “likelihood” and estimates whether a failure will occur during the design life or production. One rating indicates that the likelihood of failure is unlikely, while a ten indicates that failure is inevitable. Examples:
- 8 (High); repeated failures
- 5 (Moderate); occasional failures
- 1 (Remote); failure unlikely
- Detection (D) is sometimes also termed “effectiveness” and is an estimate of the product’s controls’ ability to detect or prevent the failure before the customer experiences the failure. Scoring indicates how likely the failure will be detected and how long this detection will take. A low score indicates that detection is certain, and will be caught during testing. A high score indicates that failure will likely go undetected. Examples:
- 9 (Very Remote); very little chance that the failure will be detected
- 6 (Low); low chance of detection
- 1 (Almost Certain); the failure will almost always be detected
A word of caution: The general rule of thumb is that the higher the RPN value, the more critical the failure mode. However, this may not always be the case. Sometimes the RPN of different cases may be seemingly obvious or identical, and you should look at the breakdown of the individual components of severity, occurrence, and detection to determine exactly how high the risk is.
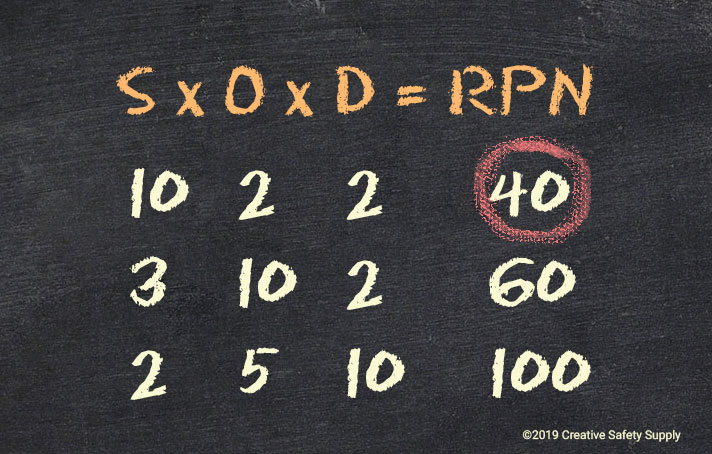
For example, severity is given the most consideration when you’re assessing risk. In this chart, you’ll see that the case which receives the lowest RPN has the highest severity score and should receive priority.
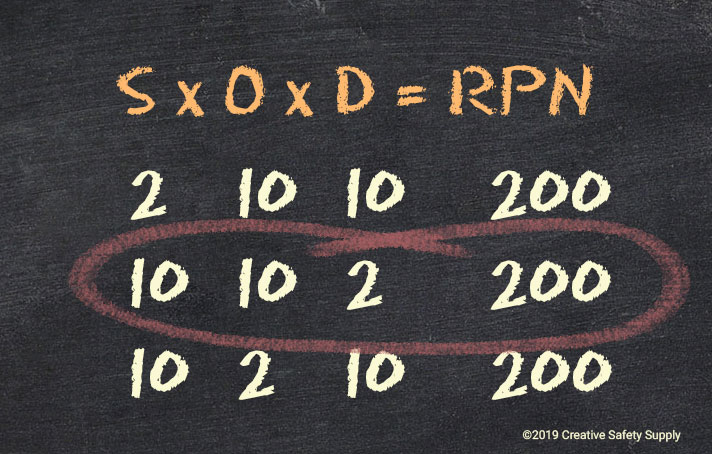
The severity and occurrence (S x O) combination is also a primary consideration since this represents the criticality of the risk. In this chart, the RPN is identical, however, the second case has the highest scores for both severity and occurrence and should receive priority.
Similar Glossary Terms
- FMEA (Failure Modes and Effects Analysis)
- DFMEA (Process Failure Modes and Effects Analysis)
- PFMEA (Process Failure Modes and Effects Analysis)
- Risk Assessment
- RCM (Reliability Centered Maintenance)
- APQP (Advanced Product Quality Planning)
- Quality Engineering
- Safety Engineering
- ESD