JHA stands for Job Hazard Analysis. This is an important part of any risk assessment where an employer attempts to discover potential hazards that exist in the workplace. This can be done to find hazards that are specific to one task, to one job type, or even to an entire facility. When done properly, the JHA will allow an employer to find hazards before they cause accidents, injuries, or damage to anything in the area.
How is a JHA Performed?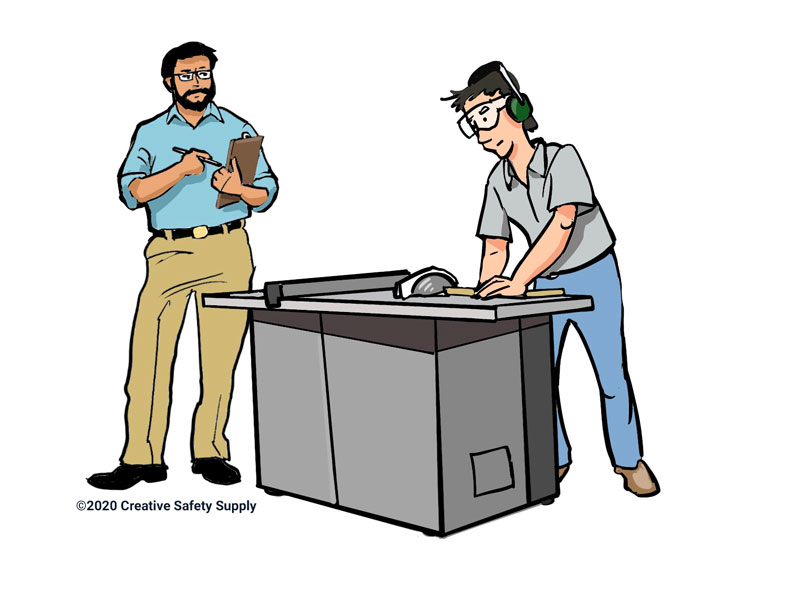
All JHA’s should include several key components that will help ensure it is able to gather as much information as possible. The following are examples of what will be included in a well-designed JHA:
- Where – The JHA should be looking at a specific area to identify what risks are present.
- Exposure – Determine what it is that is happening that is causing any potential hazard; evaluate each step of the process.
- Trigger – If a hazard is found, identify what precipitates it so that the root cause can be found and addressed.
- Outcome – In the event that the hazard occurs, what would the result be? This will help to determine the severity of the risk, and therefore the appropriate response.
- Contributing Factors – In many situations there are multiple factors that can contribute to a hazard. For example, a machine may be quite safe in most situations, but if it is raining, a hazard presents itself as much more likely.
Conducting a JHA
When performing a JHA it is important to ensure it is done correctly to get the best results possible. This should start by inviting a variety of people to participate. This should include those who work in the area, managers, safety professionals, and others. Next, reviewing all relevant accident or incident history in the area will help to give a good idea of what to look for. When ready, conducting a preliminary review of the area will help to spot areas of concern that will likely need additional attention down the road.
Once you have the preliminary report in hand, it will be time to list each potential risk and rank it based on severity, so you know where to focus future energy. Finally, conduct additional evaluations on the specific areas where there is a high potential hazard. Based on this information, steps can be taken to minimize or eliminate the hazards that were discovered during the JHA. Employers can reduce the risk of injury or illness with engineering controls, administrative controls, and personal protective equipment.
Similar Questions
- What is the difference between a job safety analysis (JSA) and a risk assessment?
- How are accident reports written?
- What is a job safety analysis?
- What is a hazard?
- What is a risk assessment?
- What is the goal of a risk assessment?
- What does a safety professional do?
- Why is it important to prevent slips, trips, and falls?
- What is composite risk management (CRM)?