Creating and maintaining an efficient warehouse can be difficult. When you have a large amount of inventory on rows and rows of shelves, it takes substantial planning to achieve successful inventory management so you know what materials you have on site at all times. Items may end up sitting for a long time, and this idleness leads to overproduction, limited space, waste, and decreased value. Luckily, rack labeling is a cost-effective and simple way to control inventory. Rack labeling facilitates the flow of items and ensures that they can be found quickly and easily. Creating a guiding system for your warehouse is one of the most important things businesses can do to maximize efficiency.
Racks are the shelving units that are used to store inventory in a warehouse. Depending on the nature of the facility or the inventory itself, a rack can be a single, long unit that goes from one side of an aisle to another. Or, a rack can be split up into smaller sections known as bins. Bins are often chosen when the products have major variations in quality and size, or there are a large amount of stock keeping units (SKUs).
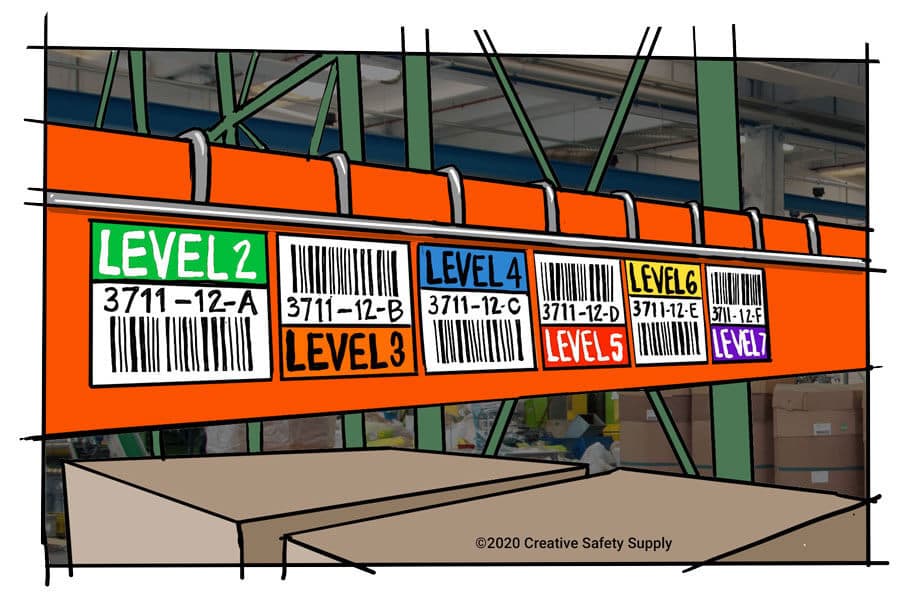
A common tool for rack labeling systems are barcode industrial labels, which are one-of-a-kind, scannable codes that convey information about the particular item. As a worker scans a barcode, they can see important information such as how much inventory there is, where it is located within the warehouse, and how long it’s been there. This way, locating the aisle number and rack number for an item takes a matter of seconds. Not only do barcodes prevent items from idling on shelves, they also allow workers to complete their jobs more efficiently.
It takes some time to develop a comprehensive and successful rack labeling system. However, understanding the basics, best practices, and your labeling options is a great start to reducing waste and making your warehouse easier to navigate.
Benefits to Rack Labeling
There are a number of reasons to consider implementing a rack labeling system, including:- It improves efficiency in inventory management and the supply chain. Keeping products moving is essential. As the flow is improved, bottlenecks are eliminated; bottlenecks are areas where work becomes stalled or backed up during the production process. To boost warehouse productivity, rack labeling addresses some of these bottlenecks (such as a worker falling behind because they could not find a product), and ensures that operations can be seamlessly conducted.
- Locating items becomes much easier and faster for workers. With a rack labeling system, workers can simply scan barcodes to immediately find the aisle and rack numbers for an item. Since the time required to locate inventory is reduced, workers can find more items and complete more tasks within a certain period of time, making their day more efficient. This also decreases the chance for human error, as the accuracy of finding the correct location is vastly improved.
- It’s a cost-effective solution. When it comes to streamlining the production process and increasing the efficiency of your business, creating a rack labeling system is one of the most cost effective options available. Labels are relatively inexpensive, yet they bring a large return on investment. This is especially true if you have an industrial label printer in-house that can create everything you need. Rack labeling prevents wastes such as lost time and overproduction, and it’s a simple solution to a variety of problems that would otherwise hurt your bottom line.
Rack Labeling Best Practices
While there are no universal requirements or standards to rack labeling, there are a few rules of thumb that will make implementing a rack labeling system easier and ensure that your labels are adapted to your unique needs. If the racks have been split up into smaller sections or bins, remember to designate labeling for each section, not just the entire racking unit itself.Best practices of rack labeling include:
- Determine your picking technique. Labeling racks provides a good opportunity to take into consideration the way that products are selected. Before you apply your labels, determine which model best fits your operations:
- Standard, in which aisles are labeled according to numerical and alphabetical order. Pickers move from location to location and may have to double back in order to retrieve the correct inventory.
- Serpentine, the more strategic option in many cases, in which pickers weave up and down the aisles. This is beneficial for fast-moving inventory or a high amount of SKUs, and pickers can operate quickly without having to double back. In this case, aisles are labeled only alphabetically. For example, AA, AB indicates Aisle 1; BA, BB indicates Aisle 2.
- Label from the bottom up. In many warehouses, a racking solution will involve high density and multiple levels. Even smaller operations often have something like two-shelf pallets. If you have more than one level of racks, it’s recommended to label from the ground up and start by giving the row closest to the ground a label such as “01”. The second row can be “02”, and so on. Using double digits accommodates the fact that you may add more levels in the future and if so, you won’t need to make changes to your system.
- If you have a lot of levels, you can use the Totem Pole rack labeling method. This stacks barcodes vertically in a location that is close to ground level, so workers can still scan everything and easily see what is on the higher shelves.
- Select the right labeling materials. In order to save time and money, take into consideration the environment of your warehouse as you choose your labels. Rack labels are available in a variety of materials, and they should match your storage conditions. For example, many industrial freezers have racks and bins, and if you have a freezer, you need cold storage supply labels that are specifically designed for cold environments so they don’t fall off or become illegible. The majority of facilities can invest in traditional vinyl labels, but you may have to look at other options if your warehouse has other needs.
- Sustain your system for the long term. Once you’ve established your rack labeling system, standardize it throughout the facility so it can be used indefinitely. This ensures efficiency for the long run and allows new workers to navigate as proficiently as experienced workers. Consistency and durability are key to this. Each rack should adhere to facility-wide standards and include durable labels that will stay easily legible no matter the environment.
Barcode Features to Keep in Mind
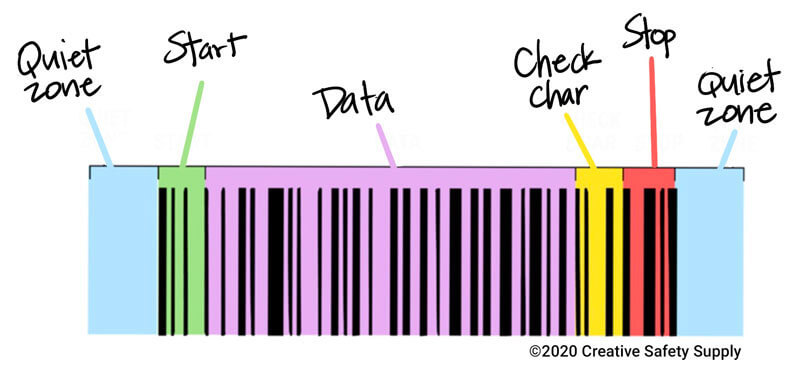
Barcodes are an integral aspect to a successful rack labeling system. Any multi-level rack system requires a set of barcode labels that can be scanned and coded with graphics and colors, which workers can understand in a single glance. Color coding is commonly used in rack labeling, to either help workers quickly identify a label or product (for example, blue labels correspond to finished goods) or to highlight important information such as the aisle number.
Three important elements of barcodes to consider for rack labeling are:
- Symbology. This refers to the spaces and lines that characterize the way barcodes are read and printed. Symbology allows labels to communicate with scanners and other barcode readers. There are a wide variety of different barcode symbologies, and you can choose which one best fits your facility’s specific needs.
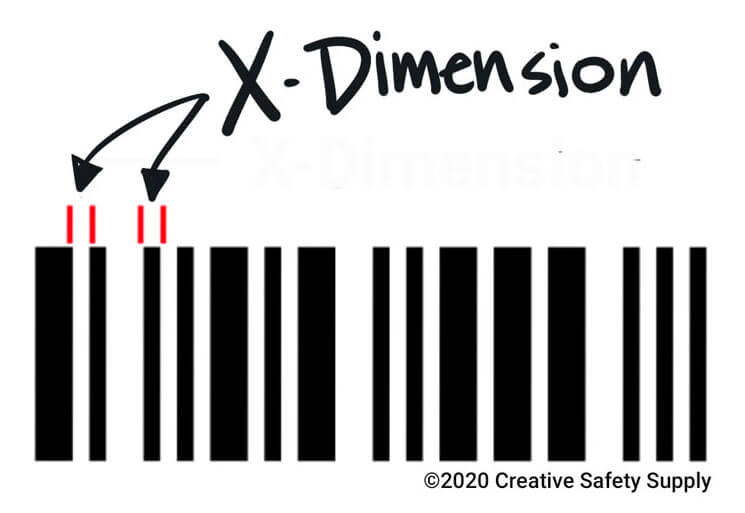
- The X Dimension, which is the thickness of lines and spaces on a barcode. This is crucial to take into account because the X dimension determines the size of the printed label, and the minimum/maximum read distances of the barcode itself. The bigger the label is, the larger the scanning distance.
- The Quiet Zone. This is the blank space that’s on either end of the barcode. Barcodes cannot go right up to the edge of the label; they need these blank spaces so scanners can get an accurate and complete read. The Quiet Zone also affects the size of your label.
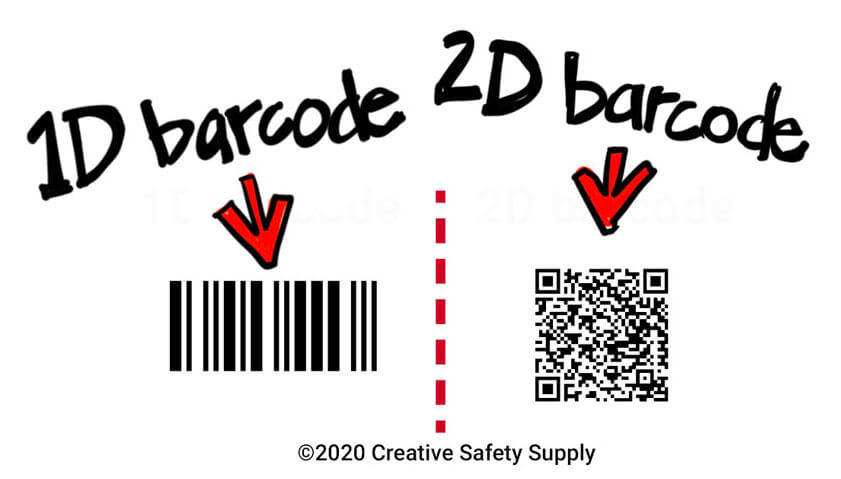
There are one-dimensional barcodes and two-dimensional barcodes. 1D barcodes have vertical lines and spaces, while 2D barcodes are square and look like television static. Warehouses typically will use 1D barcodes; 2D barcodes are more common for instances where people may use their cellphone to scan tickets or make a purchase.
Other Rack Labeling Materials
In addition to barcodes made with traditional vinyl, there are other kinds of supplies that help you organize your racks, such as:- Magnetic Labels. Labels that have a magnetic backing instead of the traditional adhesive are much easier to apply and peel away. With these, you don’t need to worry about leaving a residue behind or having difficulty getting the label off. They’re an excellent choice in situations where you need mobile labels or have a constantly-changing workplace. Warehouses often involve shifting environments, and magnetic labels handle this constant state of flux.
- Cold Storage Labels that stand up to harsh environments such as industrial freezers. These labels can withstand subzero temperatures, and you’ll find other extreme temperature labels such as ones that can survive intense heat. This saves you money in the long run, since these are more durable than traditional labels and you won’t be required to keep replenishing your supply.
- Retro-Reflective Rack Labels, which are a great solution for settings where workers must scan from a distance. By using these labels, you can scan from a range of 50 feet with long-range scanners.
- Totem Rack Labels, which stack barcodes so workers can see items that are located on upper racks. This Totem Pole approach places barcodes on a vertical post where workers can scan them easily, and they are typically color-coded to distinguish between the different rack levels.
- Floor and Aisle Signs. On top of barcodes, investing in a comprehensive visual system can help workers navigate your warehouse. Floor signs aid in locating inventory quickly, while warehouse aisle signs are large and can be seen from a great distance. Together, they enhance your rack labeling system by guiding workers to the correct location of an item.
Rack Labeling for Success
Rack labeling has a large impact on warehouse operations. It is an integral aspect to successful organizing, and organization is one of the foundations of Lean manufacturing. Having a rack labeling plan is often the key to achieving a Lean facility and reducing waste, no matter how large or small your business is. Once you develop a labeling system for your warehouse, try to implement your plans with the intention to sustain your system for the long term so your facility can experience success and efficiency indefinitely.Similar Articles
- Creating an Effective Warehouse Storage Numbering System with Barcodes
- Labeling Electrical Conduits
- Barcode Labeling
- Arc Flash Labeling (Updated)
- Introduction to Shipping Container Labeling
- Waste Water Treatment Labeling
- ANSI TIA 606-B Cable Labeling Standards
- Solar System Labeling
- Your Guide to Pipe Labeling Standards
- A Brief Overview of Key Agricultural Labeling Requirements