What Is 5S?
5S is a systematic form of visual management utilizing everything from floor tape to operations manuals. It is not just about cleanliness or organization; it is also about maximizing efficiency, quality, and profit. 5S is a framework that emphasizes the use of a specific mindset and tools to create efficiency and value. The 5S checklist guides manufacturers in observing, analyzing, collaborating, and searching for waste and also involves the practice of removing waste.
5S includes five terms that all start with the letter "S."
Origin of the 5S System
Toyota Production System
The 5S methodology traces its lineage to post-war Japan, where the leaders of a burgeoning Toyota Industries (neé Toyoda Automatic Loom Works) were seeking to reduce manufacturing waste and inefficiencies. Their solution, dubbed the Toyota Production System, encompasses a number of methodologies that would become famous in their own right, including Just-In-Time manufacturing, Jidoka, and the core concept of the visual workplace.
Initially, the Toyota Production System was a closely-guarded secret, but the massive economic boom Japan experienced in the 1980s drew intense interest from foreign corporations wondering how Toyota, the shiniest jewel in Japan's manufacturing crown, was able to build so many products, so quickly, at such a high quality level. As a gradual, international exchange of ideas began to take shape, author and ULVAC Inc. executive Hiroyuki Hirano devised the five pillars of the visual workplace, a concept that would metamorphose into the 5S methodology as we know it today.
The 5S methodology has gained importance throughout the years and is now one of the basic foundational elements of Lean, along with other Lean processes and practices such as:
What Does 5S Stand For?
5S, sometimes referred to as 5s or Five S, refers to five Japanese terms used to describe the steps of the 5S system of visual management. Each term starts with an S. In Japanese, the five S's are Seiri, Seiton, Seiso, Seiketsu, and Shitsuke. In English, the five S's are translated as Sort, Set in Order, Shine, Standardize, and Sustain.
There are five key practices involved in 5S. They are as follows:
Japanese Term | American Term | Definition |
---|---|---|
Seiri | Sort | Sort through materials, keeping only the essential items needed to complete tasks. (This action involves going through all the contents of a workspace to determine which are needed and which can be removed. Everything that is not used to complete a work process should leave the work area.) |
Seiton | Set in Order | Ensure that all items are organized and each item has a designated place. Organize all the items left in the workplace in a logical way so they make tasks easier for workers to complete. This often involves placing items in ergonomic locations where people will not need to bend or make extra movements to reach them. |
Seiso | Shine | Proactive efforts to keep workplace areas clean and orderly to ensure purpose-driven work. This means cleaning and maintaining the newly organized workspace. It can involve routine tasks such as mopping, dusting, etc. or performing maintenance on machinery, tools, and other equipment. |
Seiketsu | Standardize | Create a set of standards for both organization and processes. In essence, this is where you take the first three S's and make rules for how and when these tasks will be performed. These standards can involve schedules, charts, lists, etc. |
Shitsuke | Sustain | Sustain new practices and conduct audits to maintain discipline. This means the previous four S's must be continued over time. This is achieved by developing a sense of self-discipline in employees who will participate in 5S. |
Before and After 5S Implementation
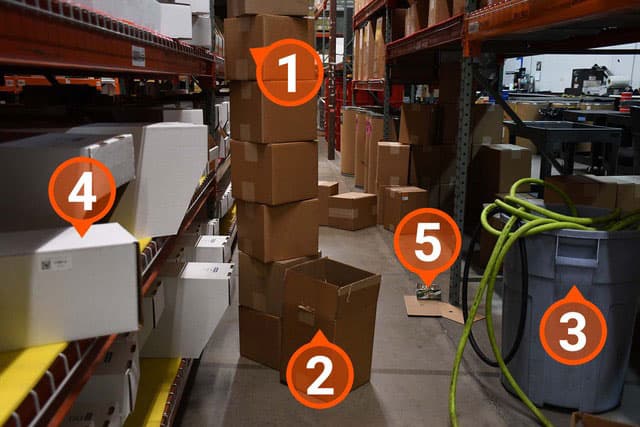
- Inventory stacked far out of reach
- Unused older inventory
- Safety hazard; boxes stacked in aisles
- No discernable organization such as barcoding, inventory dating, color coding, or naming convention
- Trash and debris allowed to accumulate
After 5S

- Uniform bins and racking
- Date tracking of inventory
- Bin contents are labeled
- Bins, racks, and floors are kept clean and in good repair
- Lighting in facility is sufficient
- Racks are low enough that ladders are not required to access inventory
Visual Management and 5S
Visual Management
Visual management, sometimes called visual control, is a method of managing a business that uses visual signals to communicate important information. These visuals can include diagrams, pictograms, color-coding, floor markings, photographs, and more. This type of management allows people to quickly understand the information being conveyed. In many cases, visual management techniques make it possible for everyone in the workplace to understand the current state of work processes. For example, a green andon light shows a process is moving smoothly, while a red light calls attention to a problem with a process.
5S is a form of visual control that focuses on organization and can improve productivity. Visual markings in a storage area can help workers return materials to their proper locations, floor markings can create boundaries around work cells, and signs on the floor can point out the proper locations for trash and recycling bins. Using visual tools like these allows a business to communicate information to workers without needing to actually say anything.
Visual Workplace
A visual workplace is a workspace where visual tools provide people with the information they need to complete their work. These visuals explain the workplace so people do not need to ask unnecessary questions. A visual workplace is often described as being "self-explaining, self-ordering, self-regulating, and self-improving" because the visual signals it uses allow it to operate with minimal extra effort from users. A workplace that uses 5S is often called a visual workplace because 5S is a method for making an organizational system visual.
5S Success Stories
- "I was teaching 5S at a supplier and while on the line, I asked what the purpose was for a certain machine (an inline nitrogen system). The supervisor said it was critical to production and needed to stay. I pointed out that the pipes connecting it to the line were cut and that it had an inch of dust on it. We found out they had not used it in years and they were able to sell it for around $100k.
In another Kaizen we had a centerless grinder with high variation. It was enclosed in a cabinet so the only point at which they knew the part was bad was after the process. The area was filthy, so we made the entire group stop and just clean for an entire day. After taking years of grease off the machine, we found two things, first, the machine was actually green, not black, and secondly there was a window where the operator could see the defect occurring."- Ben Eberhart Sr. Manager Procurement Lean Six Sigma - "In our plant, after implementing 5S on workplaces, we wanted to engage all employees in keeping 5S in their working areas. My task was to implement League 5S(a competition):
- The goal of league 5S was to engage all employees in Lean and 5S activities
- I divided plant's layout into 5S plant zones with responsible persons (production, logistics, maintenance...)
- Defined team of auditors was regularly evaluating 5S status in these zones according to questionnaire
- 5S zones were compared to each other
- People in the winning zone were awarded with prizes (once per 6 months)
After launch of league 5S, condition of 5S was improving from month to month. There are many details that Lean Coordinator must follow to keep league 5S alive and well running. 3 basic rules are: TRAINING, WELL INFORMED EMPLOYEES and PROPER AWARDING SYSTEM. For more info don't hesitate to contact me."- Miloš R.
What is the 5S methodology?
The 5S methodology is a system for handling workplace organization. It includes 5 steps known as the 5 S's that turn organization into a step-by-step system for people to follow. This methodology is often considered the foundation of Lean manufacturing because for a workplace to reduce waste and become more efficient, it needs to first be organized.
What is the purpose of 5S?
The purpose of 5S is to make a workplace function better by making it an easier place to work. This occurs by making spaces make sense; tools and materials are placed in logical locations based on who needs them, how frequently they're needed, etc. Spaces are cleaned regularly. Cleaning and organization become habits. When used correctly, 5S ultimately makes processes safer and more efficient.
What does 5S stand for?
5S stands for the 5 steps of this methodology: Sort, Set in Order, Shine, Standardize, Sustain. These steps involve going through everything in a space, deciding what's necessary and what isn't, putting things in order, cleaning, and setting up procedures for performing these tasks on a regular basis. When there's a plan for making 5S an ongoing effort and not just a one-time event, it can be sustained over time.What is the 6th S?
The 6th S stands for Safety. Some businesses choose to add this step at the end of 5S to ensure safety is a key component of work practices. Other businesses believe safety should be a part of all the steps of 5S and therefore doesn't need to be its own step. Either way, safety does play a role in 5S. Arranging spaces in logical ways, organizing tools and materials, and cleaning regularly make it easier for people to do their jobs without tripping, slipping, experiencing an ergonomic injury, etc.
How does 5S relate to kaizen?
Kaizen is a Lean manufacturing concept that refers to the ongoing process of "continuous improvement." Kaizen seeks to find small ways to improve processes over time. For kaizen to work well, everyone in a workplace participates by looking for ways their tasks could be improved and what unnecessary items need to be removed.
The goal of 5S is also to improve processes. It does so by increasing organization and efficiency. This means 5S sets a workplace up well to use kaizen. Once an organizational system exists, people can more easily look for improvement opportunities.