One of the easiest ways to improve facility safety is to utilize floor markings. Not only will the company save money by choosing industrial floor marking materials, but these tools will also play an active role in preventing worker injuries and helping improve productivity within the workplace.
Before deciding to use floor marking tools, the user must first plan meticulously. Several questions need to be asked and answered before any action occurs, or these efforts may cause more harm than good. That said, only continuous effort dedicated to improving facility safety will contribute to any future improvements at all! It all comes down to creating a safer place to work.
Benefits from All Floor Marking Strategies
Marking facility floors with signs, floor marking tape, or paint will be appreciated for years down the road. Industrial floor markings such as floor signs and floor tape are made to last the test of time within incredibly harsh industrial environments. As long as those markings are taken care of, they will protect employees.
Besides simply complying with OSHA regulations and ANSI best practice methods, one of the initial reasons companies choose to mark their floors is to reduce the number of injuries occurring in the workplace. Injury mitigation is integrated into the following three benefits that floor marking strategies provide for its users:
- Organization – The addition of floor tape and floor signs is inherently an effort to improve organization in the workplace. For example, permanent aisles and passageways specifically marked for forklifts and pedestrians keep both machines and employees in their respective lanes. These permanent aisle markings also maintain a neat space without any pathway obstructions. Work cells become neat and tidy, with objects confined to their special place. The list could go on.
- Employee Participation – Floor markings improve employee participation with safety protocol and other facility workings. This is because these markings give employees the exact information they need to be successful at that moment in time. That information may refer to PPE requirements or even an inspection checklist.
- Improved Visual Communication – The addition of any floor markings will work to improve all communication efforts. Any extra information given to employees about facility safety is helpful!
With the overall goal of injury mitigation, implementing more visual communication such as floor markings works to help employees avoid unsafe behaviors. This manifests in a way that increases employee participation with company protocol.
Increased participation in communication inherently creates a more organized workplace!
A more organized workplace also has higher levels of safe workplace behavior.
The benefits of injury mitigation, employee participation, and the creation of a more organized workspace mean there is no reason not to utilize floor markings. Facilities are safer because of floor markings.
This method creates a better workplace overall. The marking method facilitates an increase in efficiency and productivity as well as worker satisfaction and a sense of safety while working.
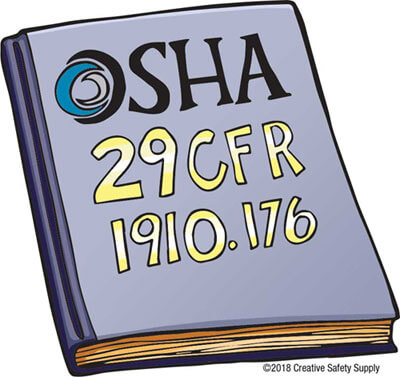
OSHA Requirements for Floor Marking Tape
Anytime anyone attempts to improve facility safety, it is necessary to consider which government regulations apply to the unique working environment. In most cases, this means looking at the standards put forth by OSHA. Floor marking regulations are addressed by OSHA under 29 CFR 1910.176.
OSHA also specifies that floor markings lines must be a minimum of 2" wide, which is essential for visibility. They can be wider, and OSHA even states that 2-6'' in width is ideal. The OSHA standards are typically easy to follow, but if they are not understood ahead of time, it could become necessary to remove and replace the markings to comply.
What about Color-Coding with ANSI Floor Marking Standards?
OSHA’s regulation 1910.176(a) states, “use of mechanical equipment. Where mechanical handling equipment is used, sufficient safe clearances shall be allowed for aisles, at loading docks, through doorways and wherever turns or passage must be made. Aisles and passageways shall be kept clear and in good repair, with no obstruction across or in aisles that could create a hazard. Permanent aisles and passageways shall be appropriately marked.”
The phrase “appropriately marked” is not as descriptive as many companies want. That means we must do some deeper digging through standard industry practices. The standard to look to in this situation is ANSI Z535. As a set of six different standards, ANSI Z535 is the recognized best practice method for many varieties of facility marking in terms of design as well as color-coding instructions.
It must be noted that many of ANSI’s older color-coding standards have been incorporated by reference into OSHA’s regulations. It is as follows, “1926.200(i) Additional rules. ANSI Z35.1-1968, ANSI Z535.2-2011, ANSI Z35.2-1968, and ANSI Z535.5-2011, incorporated by reference in §1926.6, contain rules in addition to those specifically prescribed in this subpart. The employer shall comply with ANSI Z35.1-1968 or ANSI Z535.2-2011, and ANSI Z35.2-1968 or Z535.5-2011, with respect to such additional rules.” This specification can be found in 1926.200 – Accident Prevention Signs and Tags.
The above statement instantly makes the originally voluntary ANSI standard to one that is required by OSHA!
While OSHA has not moved forward in adopting ANSI’s newer color-coding standards in Z535.1 - Z535.6, it is still seen as the best practice method for marking floors, utilizing signs, and other visual communicators within the workplace. You can find the official Z535 set here. The color standards can also be found in our extensive floor marking guide.
The 3 Facility Safety Improvements to Make
When looking to improve occupational safety, sometimes it’s the simplest tools that make the biggest difference. Improve safety within your facility as soon as possible just by putting down vinyl tape in hazardous areas, storage areas, and distribution facilities with high forklift traffic.
We have identified three inexpensive ways to immediately improve safety in your facility! Provide the following critical information to all employees in the vicinity:
- Egress Markings – Use floor tape to denote evacuation routes that lead out of the building. These markings are especially useful when they glow-in-the-dark. If the power unexpectedly goes out, employees can easily find their way out quickly and safely.
- Emergency Equipment Floor Marking – Marking the location of emergency equipment such as fire protection equipment and eyewash stations is essential. If used correctly, employees will be able to find fire extinguishers and any other piece of emergency equipment quickly so they can deal with the emergency appropriately.
- Aisle and Passageway Floor Marking – Some of the most common workplace injuries occur when there’s a lack of forklift safety. Marking permanent aisles and pathways can be done with the use of floor marking lines. With the ability to use colored floor marking tapes, employers can combine color-coded meanings with workplace safety.
The best part about floor markings is that they last a long time, making them the most cost-effective option for improving facility safety.
Prioritize Worker Safety!
To prioritize worker safety, employers must prioritize occupational risks. There are six different categories of occupational risks, those include:
- Safety Hazards
- Chemical Hazards
- Biological Hazards
- Physical Hazards
- Ergonomic Hazards
- Psychosocial Hazards
It must be noted that a biohazard risk is certainly different than an ergonomic risk. That being said, how is the employer supposed to rank these to take care of the most dangerous risks first? The quick answer is to perform a risk assessment on all identified risks within a facility. Any occupational risk should take precedence over risks associated with topics such as financial risk since employees are by far the most important asset of a company.
One of the first steps in facilitating workplace safety for these hazards and risks is finding a way to prevent them from happening. If there is still risk present, the employer will want to provide them with supplemental communication about the risk in the form of signs, floor tape, and training.
To truly understand what it takes to fight risk in the workplace, become familiar with the Hierarchy of Hazard Controls. This strategy will lay out the right order in which to try and control any hazards presenting themselves in the workplace.
Marking Physical Hazards with Floor Tape
In addition to using floor markings for the sake of helping guide people through a facility safely, it is also possible to use markings to identify specific hazards that should be avoided. Applying floor marking tape around a particularly dangerous machine, raw materials storage, near places where falling objects may occur, or for any other hazard, are great forms of visual communication.
The tape around these areas should be colored or patterned uniquely so that everyone can immediately recognize what the markings mean. In this image, black and yellow patterned markings are used to identify a gap in the floor where a moving machine works. Those working in the area will be able to identify the risk as they approach and make sure to stay away from the danger.
Different Types of Floor Tape to Use
When considering floor markings for floor safety, there are two main options to consider. The first, and most popular option for many types of facilities, is going to be floor marking tape. There are many different types available depending on the specific needs of a facility. Anti-slip tape, glow-in-the-dark tape, reflective tape, and others are all available for use. You can even get pre-cut shapes made from floor marking tape to help make the whole process easier.
While it isn’t exactly floor tape, the other option is floor marking paint. Paint can be applied easily in most environments, though it does need time to dry completely. Paint can be applied using a simple roller tool, stencils, or a machine depending on the environment.
Consistency is Key for Floor Marking
One of the most important things you can do when planning floor markings for facility safety is to ensure the same standards are used throughout the company. This is most important when applying floor markings since employees will often have to work in multiple different areas in the building.
This rule of thumb also applies to companies that have facilities in different locations. Some businesses, for example, have a manufacturing building and then a warehouse. The same marking strategies must be used in both locations to avoid confusion and ensure the best results for improved safety.
Floor Marking Becomes Easy with Helpful Resources
As the leaders in visual safety, we are the Lean experts you can trust! Creative Safety Supply has countless resources when it comes to floor marking, especially those relating to safety. Brush up on standards and regulations with our numerous educational resources about floor marking here. We also have a free downloadable OSHA Floor Marking Guide that you can use as a reference for all your floor marking projects.
Lean Manufacturing Products that Help
With the right tools and the right information, you’ll be able to find the right tape to label all the physical hazards within your workplace such as electrical panels, improve forklift safety by marking traffic lanes, and even mark emergency equipment such as fire protection equipment.
To finish it off, we also make our very own industrial floor marking tape! SafetyTac®is one of the most durable floor marking options on the market. With our tape, you’ll be able to create a tidy workplace that keeps workers informed of their surroundings.
You can also check out our other floor marking options here. You’ll find floor signs, shapes, and even glow-in-the-dark floor tape!