Determining Hazards and Keeping Employees Safe
A Job Hazard Analysis (also known as a Job Safety Analysis) is a process used for reviewing specific jobs or tasks in order to identify, and then address, safety hazards. Once potential hazards have been determined, controls can be put in place to reduce the chances of an illness or injury occurring because of these hazards. Often, this analysis is the first step to a risk management program.
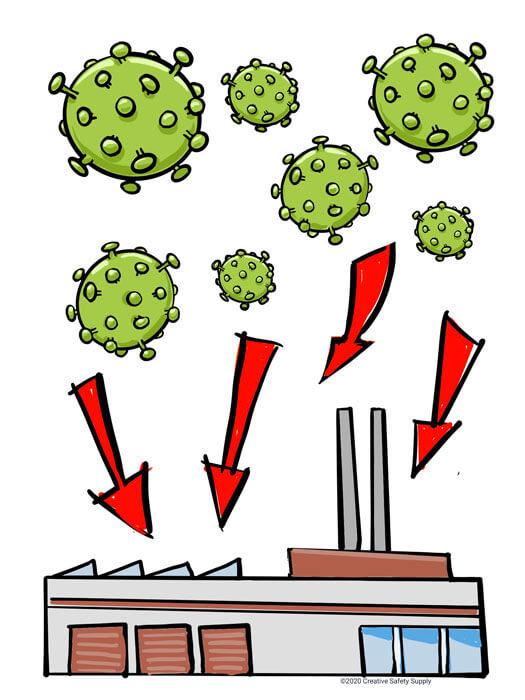
As the novel coronavirus pandemic continues to make its impact around the world, the nature of the workplace is changing. For the first time, many businesses are conducting hazard analyses to determine the risk of their employees contracting and spreading COVID-19, the dangerous respiratory illness caused by the coronavirus. Certain jobs—for example, completing administrative work in an office—that wasn’t previously considered to be hazardous is now being evaluated to determine risk.
Job Hazard Analyses (JHAs) are effective tools to mitigating risk in your workplace. Since most organizations don’t have the capacity to evaluate every single task, it’s important to prioritize your analyses based on:
- The potential for severe illness or injury
- Illness or injury rates
- The risk of human error leading to an incident
- Tasks that have recently been changed or introduced (for example, many employees are now using hazardous chemicals to disinfect frequently touched surfaces)
You may find yourself conducting a hazard analysis for the first time, or may be adjusting your risk management program to address the coronavirus. Either way, a Job Hazard Analysis is the first step to ensuring your employees are fully protected as the pandemic’s impact continues.
Steps to Conducting a Job Hazard Analysis
Before implementing any hazard controls, the risks that are present in your given situation must first be determined. By conducting a Job Hazard Analysis, you can identify risks in your workplace, including the coronavirus, and understand which controls will be effective. Ask yourself if workers can socially distance, if the task at hand requires close contact with the general public, or if there are shared items and tools. What may be done to mitigate this risk?
Completing a Job Hazard Analysis involves these steps:
- Observe the job or task you will be analyzing. This is a good opportunity to implement Gemba, also known as “the actual place,” in which supervisors observe frontline operations. You can break the task down into small steps and take your time analyzing each step. It’s often helpful to talk with workers during the observation to gain insight.
- Identify potential hazards. These hazards may range from physical hazards, such as objects that may fall from overhead, to chemical hazards such as using harsh chemicals for cleaning. The spread of respiratory illnesses, including COVID-19, is also a hazard, as it poses a threat to workers’ health and safety. Look for the root cause of these hazards; ask yourself how they occur, what the contributing factors are, and what the consequences may be.
- Rate each hazard according to priority. You can calculate a Risk Priority Number (RPN) in order to assess the severity of each hazard, how often it may happen, and the probability of it happening, in order to determine which hazards should be mitigated first. The ones that are most severe and are most likely to happen must be addressed as soon as possible.
- Implement hazard controls. Once you’ve made observations and determined which hazards are the priority, initial recommendations may be made. A helpful starting point to these recommendations is to consult the Hierarchy of Hazards, a widely used risk management tool which helps you determine the proper response to a given hazard. The controls you implement will vary based on the nature of the hazard, and whether it can be completely eliminated.
It’s important to note that a JHA should be completed by a team of employees that includes people who are familiar with the actual job in question. Typically, a JHA team is made up of one safety manager, one supervisor, and two or three frontline employees.
The Hierarchy of Hazard Controls
Once you’ve determined hazards, how do you respond to them? The Hierarchy of Hazard Controls is a helpful place to start. Not only is this hierarchy recommended by OSHA as a safety improvement step for all industries, the CDC and NIOSH have established an official version of the Hierarchy of Controls. Each measure of control is listed in order of effectiveness:

- Eliminating the hazard completely is the most effective means of control. This measure is most ideal—however, many hazards including the coronavirus are not possible to fully eliminate.
- Substituting the hazard is the next best solution. You can substitute the risk with something less dangerous. For example, harsh cleaning chemicals can be exchanged for non-toxic cleaners that may take more effort to use but are just as effective.
- Engineering controls, which may be implemented to control the hazard. For example, many workplaces are increasing ventilation in their indoor spaces so fresh, clean air is provided in an attempt to prevent contaminated air.
- Administrative controls, which are rules and regulations meant to minimize risk and reduce the chances that an incident will occur. Social distancing and keeping at least six feet of space from other people is an administrative control.
- PPE, Personal Protective Equipment, is your last resort; PPE is meant to protect workers if the hazard cannot be eliminated or reduced. PPE that is recommended by the CDC for slowing the spread of the coronavirus includes face masks/face coverings and gloves.
The Hierarchy of Hazards provides insight into methods you may use to minimize danger, and helps you take the best action to keep people safe. Take note that more than one hazard control can be used at once; in your workplace, you can provide face coverings to your employees, strictly enforce social distancing, and increase air circulation.
Using Hazard Controls for the Coronavirus
For further recommendations on implementing workplace controls to reduce the risk of exposure to the coronavirus, you can consult OSHA’s “Guidance on Preparing Workplaces for COVID-19,” which recommends the hierarchy of controls. Although it’s not possible to eliminate the hazard of COVID-19 during an outbreak, there are effective protection measures you can take. In most cases, you will need to implement a combination of measures, tailored to your unique workplace, to protect workers.
Everyone Has a Role to Play
Safety is everyone’s responsibility, no matter the industry. Each day, employers, supervisors, and employees must do their part to ensure their workplace is safe. Especially in the case of respiratory illnesses such as COVID-19, it’s important to maintain an awareness of personal responsibility for controlling risks.

Make sure everyone understands what their role is when it comes to identifying hazards in their workplace, whether it’s a fire hazard or an instance in which they can’t socially distance. Everyone should also be familiar with the actions they can take when it comes to implementing hazard controls. Not only does this prevent incidents, it also provides open communication between employees and their management.
Managers and employers should:
- Fulfill their responsibility for ensuring that jobs are as safe as possible. Under OSHA’s General Duty Clause, employers are required to provide a place of employment that is free from recognized hazards.
- Provide the proper tools and equipment to employees, especially tools that reduce the risk of hazards. This includes personal protective equipment; employers are responsible for providing each employee the PPE they need to complete their tasks.
- Ensure that the correct processes and procedures are in place, and that each employee has the ability to follow them. This involves overcoming any language barriers and implementing labels or signs to ensure communication.
Employees should:
- Be familiar with their employer’s safety systems and options for hazard mitigation, as well as the order in which these options should be implemented.
- Adhere to control measures that have been established by a hazard assessment.
- Ensure they are using all equipment and tools (including PPE) in the way it was designed to be safely used.
- Refrain from taking shortcuts around safety steps and creating hazards themselves.
- Understand they are responsible for reporting new hazards that arise so a new JHA may be conducted, and the hazards will be addressed.
Hazard Mitigation During a Pandemic
Companies around the world conduct hazard analyses and use the Hierarchy of Controls as an effective aspect to successful risk management or their safety improvement program. Now more than ever, it’s important to ensure you have the right solutions in place to mitigate hazards and keep workers safe. Your employees should be familiar with this concept, as well as which controls are in effect to reduce the spread of respiratory illnesses such as COVID-19. By conducting a Job Hazard Analysis and communicating with your employees about the ways you are implementing hazard control, you can help ensure workers do not put themselves at risk for any type of danger in your workplace.
Similar Articles
- OSHA’s Guidelines to Protecting Employees from Coronavirus
- Hierarchy of Controls [Hazard Exposure + Prevention]
- Job Safety Analysis
- Addressing Biohazard Safety in the Workplace
- Cleaning the Workplace During COVID-19
- Hazard and Operability (HAZOP Analysis)
- Returning to Work Safely
- Understanding Risk Assessments in the Workplace
- Workplace Safety Inspections & Audits