- Why is Construction Safety Important?
- What are the Most Common Safety Hazards in Construction?
- What Can an Employer Do to Reduce Existing Hazards?
- Safety Precautions for Construction Sites
- Electrical Safety at Construction Sites
- Commonly Used PPE at Construction Sites
- Crane Safety
- Other Safety Standards to Be Aware of
- Final Construction Safety Tips
Out of all occupations in the United States, construction workers encounter some of the most hazardous conditions. 2019 had the highest number of private construction industry deaths at a total of 1,061 fatalities. That year, the nation saw a 5% increase in workplace fatalities since 2018. As upsetting as those numbers are, every one of those incidents could have been prevented entirely if established rules and regulations were recognized and followed in earnest. In short, the people who work in this type of environment must live and breathe safety.
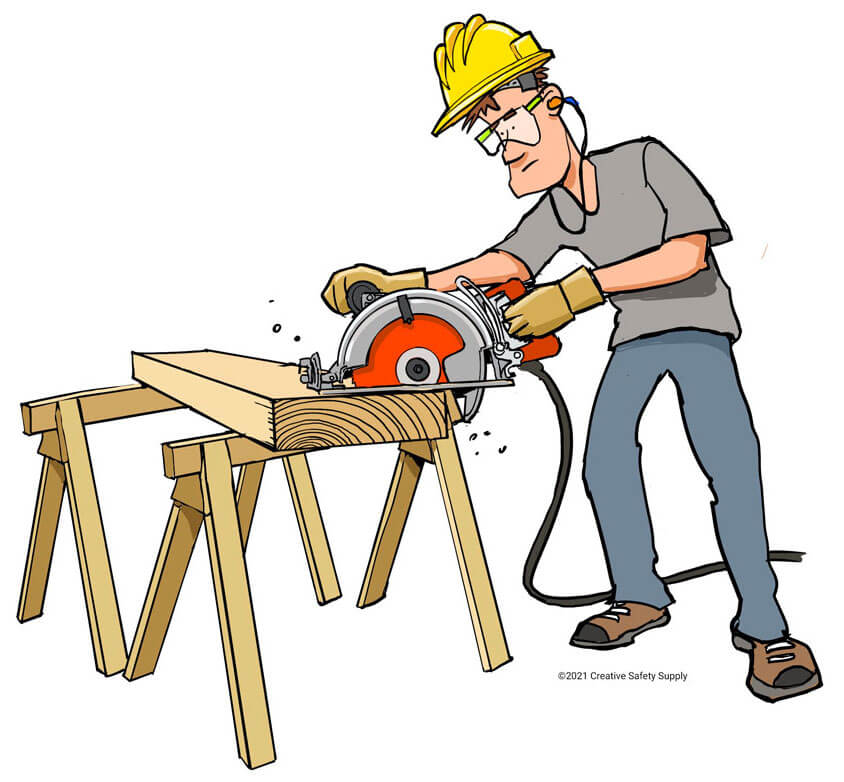
Why is Construction Safety Important?
Some managers and employees take construction safety for granted. It often takes a little bit more time, effort, and money to adequately create a safe environment for all employees and the community. As a result, it can be tossed aside and forgotten about until something catastrophic happens and people become injured, or worse, fatally injured. With that being said, the obvious answer as to why construction site safety is important is because it saves lives.Saving lives is the epitome of construction safety, but the next most important result of following regulations is saving the business as a whole. When referring to construction site safety through a business lens, there are quite a few other reasons why these companies should want to minimize deadly incidents. Those are as follows:
- Profit Loss – Accidents often impair construction workers to the point where recovery times can reach up to weeks or months. In the worst-case scenario they become permanently disabled. When this happens, aside from losing precious time from an experienced employee, the employer’s insurance premiums may skyrocket. When insurance costs go up, so does the price tag for hiring these construction companies, which may result in less job opportunities. Accidents cause monetary loss in the long run.
- Productivity Loss – As we know by now, accidents resulting from a lack of adequate safety procedures often lead to injuries. Those injured employees and any damaged equipment are incapable of getting work done for obvious reasons. Furthermore, both people and equipment used in these kinds of specialized environments are very difficult to replace, which can delay production even more.
- Workers’ Compensation and Medical Bills – If it has been determined that an accident occurred due to employer negligence regarding safety protocol, then any construction workers that were injured will most likely require compensation. These payments include lost wages, medical treatment, ongoing care costs, and even compensation for disability leave. All of these, referred to as workers comp, come from the employer’s insurance policy.
- Investigation – Every serious workplace accident will most likely be investigated by authorities to determine who is at fault. If it was due to a lack of safety, the construction company may be fined and the one in charge may even face time in jail for endangering their employees. This can be prevented if all the correct safety precautions are followed.
- Negative Publicity – Delivering finished projects on time, being honest with work, and doing a good job help a construction company’s reputation. However, accidents can quickly demolish those aspirations. If a construction company is known to not be as safe on the job as they should, project managers or business owners may not want to hire that particular construction firm.
- Worker Distrust – Unsafe environments in the construction industry often result in a lack of trust between employees and their employer. Employees put their lives on the line every day and with that they expect the employer to care about their well-being and safety. Distrust breeds discontent, leading to a divide between employers and employees that is dangerous for both parties.
There are countless reasons why construction safety is important. The above reasons are only a handful, but some of the most important. Staying up to date on standards, regulations, and building trust with employees and the community are all essential to keeping everyone safe, and to continue doing business as usual.
OSHA Construction Standards
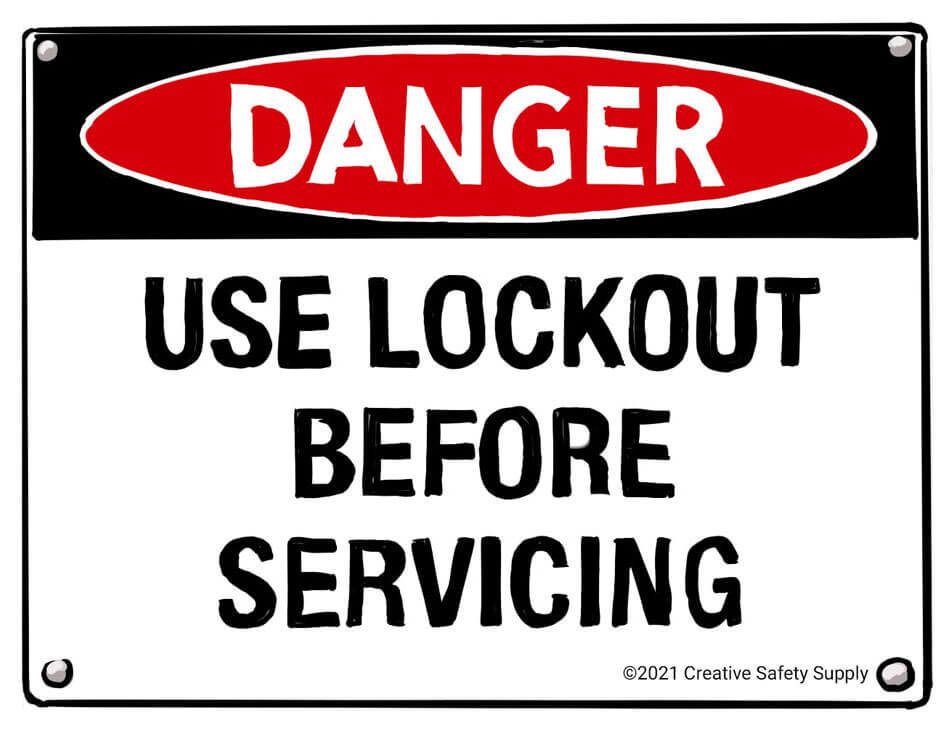
There are definitely too many construction regulations put forth by OSHA to name every single one of them here. With that being said, here are the top ten most cited regulations that OSHA doles out to worksites after a routine inspection. They are as follows:
- Incorrect use/lack of fall protection, 29 CFR 1926.501
- Not adhering to the Hazard Communication Standard, 29 CFR 1910.1200
- Failing to use scaffolding safely, 29 CFR 1926.451
- Failing to use Lockout/Tagout 29 CFR 1910.147
- Incorrect use/lack of respiratory protection, 29 CFR 1910.134
- Failing to follow ladder regulations, 29 CFR 1926.1053
- Failing to follow powered industrial truck regulations, 29 CFR 1910.178
- Failing to implement fall protection training, 29 CFR 1926.503
- Failing to follow machine guarding regulations, 29 CFR 1910.212
- Incorrect use/lack of eye and face protection, 29 CFR 1926.102
There are two parts in CFR 29 that employers must be familiar with—Part 1910 for General Industry and Part 1926 made specifically for construction requirements. The reason employers must be familiar with both rather than just Part 1926 is because there are some hazards in Part 1910 that also apply to construction safety. “How will I know which regulations apply to me?” you may ask. Go through those regulations and if you still have questions you can present those to the local authorities or OSHA themselves. There’s no shame in asking questions to make sure your employees stay safe on the job.
What are the Most Common Safety Hazards in Construction?
When working on or around construction environments, everyone needs to be aware of what are called the “fatal four.” Seems a little ominous, but that phrase refers to the four most common dangers associated with construction sites. In fact, when all four instances are combined, they account for more than half of all fatalities in the construction industry. They are the following:
- Falling – Improper use of fall arrest systems can result in falls from only a few feet up to hundreds. This is the most dangerous of the fatal four, and the most common. Slips and trips are also not one to play around with, they can break bones, tear ligaments, and be the source of head trauma.
- Being Struck by an Object – Hard hats are used for a reason! Being struck by falling objects or other projectiles of varying size and weight can happen anytime at construction sites. Wearing the right protective gear for the task is essential. It is also good to note that there are different classifications of hard hats and steel toed boots that must be looked into before choosing.
- Being Crushed by Heavy Machinery – Machine guarding is often seen on stationary equipment at manufacturing facilities. However, more often than not, tools and machines at construction sites are primarily operated by people rather than being a fixed piece of machinery. The correct training, self-protection, and self-awareness information must be given to employees. This will help to prevent them from using the tool incorrectly or stepping in the way of someone else operating a forklift, crane, or backhoe.
- Being Electrocuted – Construction takes care of more than just concrete work, wood working, and building in general. Electricity is a central part of how things are run in all communities that have access to it. Electrocution is not rare in these kinds of occupations. There are powerlines everywhere, and one wrong move while operating a crane can take lines down in an instant. For that reason, it is always necessary to again be aware of the surroundings. If an accident does happen, let an electrician take care of it. They are specially trained to work with electricity, are the only ones authorized to do so, have the right tools, and can finish quickly rather than someone who is more familiar with operating heavy machinery.
The above four are the most common reasons for fatalities occurring in construction accidents. However, there are other risks that employees encounter while on the job. For example, they could have become injured but were working alone. Without anyone around to check and see where this person was, they may die from the injuries they sustained. As a solution to that, try having workers be in pairs while performing tasks or even give them a way of contacting others in the event of an accident.
Whether it be communication regarding an accident or communication involving training on the employer’s end, being able to collaborate and solve problems as a team is essential for this kind of occupation.
What Can an Employer Do to Reduce Existing Hazards?

In many instances, employers in the construction industry solely use personal protective equipment to protect their employees. This is the exact wrong thing to do as a matter of fact. Think about it this way, wearing a hard hat, gloves, and steel toed boots won’t help workers in the event that they encounter a tool that doesn’t have a safety guard. The risk of using that machine is still blatantly evident, and nothing has been done to minimize employee risk.
Let’s talk about the Hierarchy of Hazards. This tiered approach to minimizing hazards at a construction work site is essential for using PPE effectively. Normally depicted as a triangle, it can face either right side up or upside down and includes five sequential hazard minimizing techniques. They are as follows:
- Elimination of Hazards – By far the most effective way to prevent accidents from ever occurring is by working to eliminate any and all hazards entirely.
- Reduction of Hazards – Next down the line is a reduction of the existing hazards. This should be done if the hazard cannot be eliminated or replaced all together. Consider adding more machine guards, updating old machinery to options that have more safety features, or anything else that may help get rid of unnecessary risks.
- Implementing Engineering Controls – After attempting the first two options and the hazard is still present, try using engineering controls such as modifying the existing system to provide better protection to employees.
- Implementing Administrative Controls –This takes the form of rules, operating procedures, the implementation of safety signs to alert workers. All of this should be put in place by the employer.
- Personal Protective Equipment – Last but not least comes the PPE. With all the hazardous conditions minimized in the workspace, the employer now has to choose the appropriate PPE for their employees. Now that the environment is much safer for those employees, the PPE provides protection that will likely save their lives in the event of an accident.
By following the hierarchy of hazards, the construction site should become free from the more dangerous risks. The next part that comes into play for reducing hazards and promoting site safety is reinforcing the adherence to all new protocols, procedures, and safety rules.
Safety Precautions for Construction Sites
Accidents and emergencies can happen even if all the rules are followed. In these instances, it’s best to be prepared for the worst. But that can’t happen without an Emergency Action Plan. That’s correct, it’s not just manufacturing or distribution facilities that need an EAP. Construction sites fall under this particular OSHA law as well. An EAP is a safety precaution in the sense of keeping employees safe after an emergency has occurred. Think of it as a “get out and get to a safe place” plan, naturally defensive in nature rather than fighting against the emergency.
Covered in CFR 29 1926.35, OSHA states that every EAP should be in written form to allow for easy access to those who need it. For companies with ten or less employees the EAP can be communicated orally.
Every one of these plans requires that employees know about:
- First aid
- How to report an emergency
- How to evacuate and what evacuation routes to use
- The different types of emergencies
- The employees’ emergency evacuation responsibilities
- Where to go to after evacuation
- The person to contact for all this information
All of this content should be reviewed in training sessions that specifically go over emergencies. It is also prudent to include re-training sessions for employees that have been there a long time. Refresher courses help to keep all that information up to date and relevant.
Having an EAP is a standard business practice, and requires, for almost all facilities, even offices. Having that safety net of knowing what to do during an emergency situation is crucial to be able to save the lives of employees. Aside from this bigger picture emergency situation, let’s take a look at some of the individual precautions that employees can take themselves to make sure they are as safe as they can be.
Electrical Safety at Construction Sites
Whether it be contact with overhead powerlines via heavy machinery, ladders, scaffolding, or human touch, the construction industry represents all 52% of electrocutions that occur in the workplace. Preventing these accidents is a matter of following the right precautions before or during a task.
Now, there are a few OSHA regulations to be familiar with when working around electrical equipment. Covered in Part 1910 of CFR 29, sections 1910.137 for Electrical Protective Equipment and 1910.269 for electric power generation, Transmission, and Distribution are the two most important ones to know.
Aside from the electrical standards that are required by law, there are a handful of electrical safety tips and precautions that everyone can take to make sure they stay safe around power sources. Those are:
- Provide thorough training and appropriate PPE for employees that work with or around electrical hazards
- Remember to conduct electrical testing and have that equipment on hand
- Have inspections occur on a regular basis as a part of normal precautions
- Complete a risk assessment to identify electrical hazards
- Have all the appropriate signage to make sure employees know of the danger
If all the appropriate electrical safety precautions are taken, then employers have done their duty when it comes to protecting their employees from electrical related injuries or death.
Commonly Used PPE at Construction Sites

As for the more recognized precautions that constructions workers take while on the job, PPE is the one that takes the cake. Everyone has seen men and women wearing hard hats, gloves, thick boots, and reflective vests while driving by construction sites. But these common items have a lot more to them than meets the eye.
Hard hats, eye protection, respiratory protection, hearing protection, gloves, and work boots are only some of the types of PPE available, and they all have different ratings that meet different protection requirements. Some of the more specialty PPE equipment includes fall protection harnesses and welder’s gear. Regardless, this type of equipment is always chosen by the employer as well as paid for by the company, with a few exceptions. Overall, choosing the right PPE is choosing between possibly exposing employees to hazards or ensuring that they get to go home safe after every day.
Crane Safety
Another pinnacle of construction safety revolves around crane hazards. The largest mobile crane, affectionately called Big Blue, can reach up to 700 feet tall and can move 2,600 tons with ease. Now that is one massive machine, and just like they say, “with great power comes great responsibility.” A little cheesy for sure, but it does stand true with these large pieces of machinery. Operators must be certified, and other personnel must be aware of the common hazards while working around this type of equipment. Those hazards are as follows:
- Electrical Hazards – Cranes have the capability to knock over powerlines easily. Everyone must be aware of their surroundings.
- Falling Materials – Debris can often fall after being lifted by cranes. This is why it is essential to wear the right protective gear such as hard hats and steel toed boots.
- Overloading the Crane – Cranes have a finite ability for lifting. It all depends on how large the counterweight is and how strong the crane is built to be. Overloading these machines can be disastrous, tipping one over can mean the end of a project.
- Pinch Points – As cranes move, they create pinch points. These can easily crush a person’s arms, legs, hands, or entire body.
- Accidentally Dropped Loads – Never be directly under a crane that is currently at work. Dropped loads can easily crush other machinery, vehicles, and people if something goes wrong.
Employees must use the appropriate PPE, perform crane inspections regularly, use safety signs, provide training for employees, and use hand signals to direct crane operators in noisy areas. All of this works in tandem to prevent crane accidents from occurring in the first place.
Other Safety Standards to Be Aware of
Many of the standards governing the use of PPE come from ANSI and the NFPA. OSHA recognizes these standards as consensus standards which means companies can still be cited for not protecting their workers as specified in those recommendations.
Aside from following PPE related standards, building owners must prepare their construction work by following the NFPA 241 standard. This document focuses on safeguarding structures during construction, alteration, and demolition. That is primarily done by removing combustibles in construction environments. There is good reason for this! On average, there are about 4,000 construction related fires every year. These dangerous incidents often cause both civilian and employee fatalities and result in millions of dollars in damage to the property.
Creating a construction fire safety plan in the construction industry begins with applying for the plan at the same time as all permit applications have been turned in. The Fire Prevention Program Manager (FPPM), hired by the general contractor, owner, or another third party, is in charge of this plan. It must stay up to date in accordance with changing conditions. These plans often include the following:
- The project means/methods
- Any and all hazards
- The mitigation tactic for those hazards
- Logistics
On par with NFPA 1 and the IFC, NFPA 241 is an essential component to construction safety when thinking about fire prevention. The standard is available for free on NFPA’s website, go take a look!
Final Construction Safety Tips
Overall, construction safety is a multifaceted effort to keeping all employees safe while on the job. As long as the standards and OSHA laws are applied, those working in the safety industry will be good to go on all of their projects.
In addition to the above, try implementing some 5S techniques or even put up some more visual safety components such as construction safety signs or QR code labels for training, machine manuals, and information in general. Extensive direction, training, and spatial awareness are all good attributes to have in a safety conscience environment.
Similar Articles
- Safety Protocols for Construction Sites
- OSHA Facts [Updated Statistics 2019]
- Crane Safety
- OSHA Ear Protection Requirements (Standards for Hearing Safety)
- OSHA Accident Reports
- Fall Protection in the Workplace: OSHA’s Guidelines
- Understanding the OSHA 300 Log and Other Incident Paperwork
- OSHA Safety Sign Requirements [1910.145]
- Improving Workplace Electrical Safety