There are different ways to assess your workplace and determine how effective the current safety and health procedures are. Two main methods that address different aspects of workplace safety management are safety inspections and safety audits. Inspections are a systematic and thorough examination of the physical conditions of the workplace, with a formal process of documenting any hazards or unsafe practices. Audits are similar, but have a different focus. There are two major purposes to audits: to identify any weaknesses in the current safety program, and to determine whether the company is in compliance with applicable safety regulations.
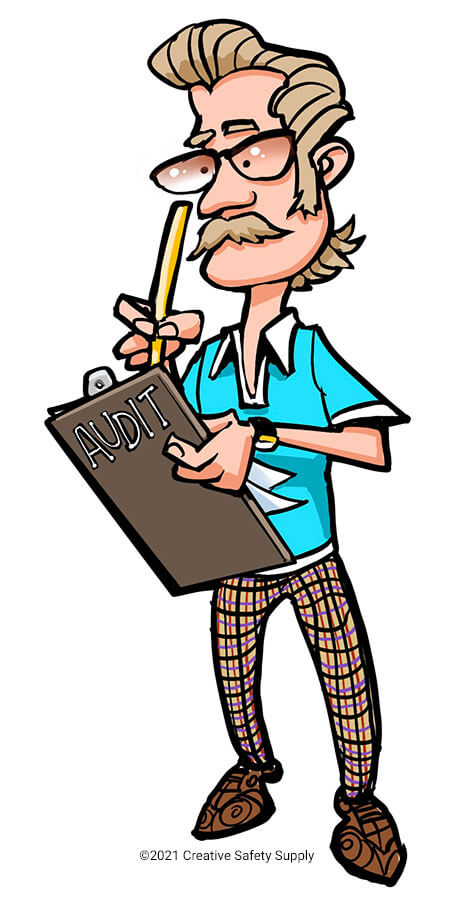
The ultimate aim of both these methods is to continuously improve safety in the workplace and overall reduce injuries, illnesses, and fatalities. Although different, they both help businesses establish a strong safety culture. Inspections are conducted internally because they require the input of someone who is familiar with the workplace, while audits are conducted externally because they require an outside perspective and need someone who can make considerations without bias.
What is a Safety Audit?
A safety audit is an activity where the effectiveness of a workplace’s health and safety program is evaluated. Ultimately, an audit determines whether the goals and standards set forth by the facility’s specific safety program are achieved during daily operations. Safety audits aren’t used to identify hazards or unsafe practices; instead, audits gather information about a safety program that should be already in place, and identify areas for improvement.
Safety audits are commonly conducted to:
- Address a recent safety concern and ensure that the current health and safety program is sufficient enough to keep workers from getting injured
- Follow up on a recent incident to determine whether the injury or illness was a one-time accident or if there is a risk it will happen again
- Ensure that the company is meeting legislative requirements concerning safety standards
- Promote the company’s safety culture and encourage constant engagement in safety-related activities
Audits are typically conducted by someone from outside the company who is familiar with applicable safety standards (i.e.: an OSHA safety inspector, or a health and safety professional). This person will review records of incident reports, observe operations, and interview employees either over several hours or several days, then provide the results of their findings. It often takes an external point of view to spot any hidden problem areas within the safety program.
Based on the results of the safety audit, an organization should determine recommendations for improvement. On top of ensuring that a business is in compliance, safety audits can also correct oversights that may eventually cause an incident in the workplace. Many facilities have found that safety audits are an essential tool to uncovering weaknesses, and they conduct audits as the first step to creating a new and improved safety plan.
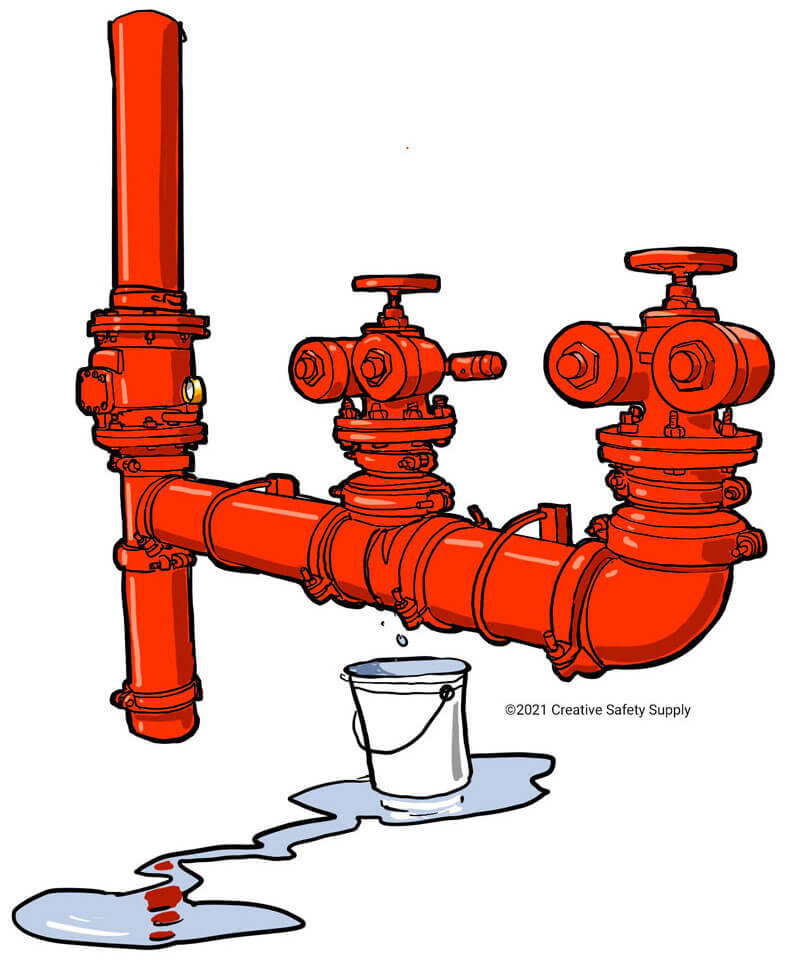
The Difference Between Safety Audits and Inspections
It’s easy to get confused between a safety audit, and a safety inspection. While they both make sure that operations are carried out as safely as possible, they are not the same thing. Understanding the difference can help provide your business with the type of safety management it needs.
Safety inspections:
- Observe workplace practices and determine whether there is any aspect to operations that is unsafe
- Identify existing and potential hazards
- Establish the procedures to eliminate these hazards, or otherwise guard/protect against them
- Examine equipment and determine whether safeguards are sufficient
- Are conducted by internal personnel or someone who otherwise is familiar with operations; care should be taken to ensure employees don’t inspect their own work area or department
Safety audits:
- Evaluate how effective the inspection process is
- Analyze current safety systems, including the employee training program, that detect hazards and eliminate, circumvent, or control these hazards
- Determine if the safety program meets the company’s goals (ex: reducing the occurrence of injuries)
- Are conducted by external personnel; an outsider’s perspective provides a more objective assessment of an established safety program
Ultimately, inspections focus on identifying and eliminating hazards and audits focus on overall safety management. To determine which needs to be conducted at your workplace, ask yourself: What do you need to focus on? Do you need to evaluate the existing and potential hazards, or do you need to evaluate the process which you’re already using to handle hazards? Both of these practices are crucial to your organization.
There are many ways to improve safety. Workplace inspections and workplace audits both have their place; you just need to understand which one is most appropriate and how to make the most out of your findings.
Completing a Site Safety Check
Whether your facility conducts a safety audit or inspection, it helps to critically examine the workplace and identify any needs for corrective action. Consistent safety checks should be a significant aspect to your company’s occupational health and safety program, and they should follow a standardized format. Take the time to determine exactly what they will examine, which areas are to be included, and how often they will be done.
Each inspection should take into account all the elements of your workplace: its people, equipment used, processes, and environment. Elements that may develop into unsafe conditions should receive particular attention, and it’s helpful to include areas where hazards may exist even though no work is conducted there, such as parking lots, locker rooms, and bathrooms. The personnel who examine your workplace need access to paperwork such as a floorplan or diagram of the area, a list of hazardous products (or a chemical inventory), an equipment inventory, incident reports, and reports on previous inspections to determine whether any past recommendations were implemented effectively. The importance of listening to workers and supervisors should be emphasized, since they know the area better than anyone else.
The frequency of inspections depends on several factors. Site safety checks will be conducted more frequently if you have a large size of operations, there are high-risk areas onsite, new machinery is introduced, or there have been incidents in the past. Applicable legislation may require a certain number of planned and formal inspections, depending on the nature of equipment and work processes.
Continuously Improving Workplace Safety
Once a safety check has been completed, it’s important to analyze the results. Inspection and audit reports can show whether there’s a need for improved safe work practices or more employee training. They also may indicate specific areas or equipment that require further, more in-depth analysis. Ultimately, reports provide insight on which areas are unsafe and why. From there, you can determine steps to take and establish priorities for corrective action. This not only helps you get into compliance, but also relates to injury prevention as potential problems are spotted and resolved before they lead to an incident.
Safety audits and inspections are integral to continuously improving the workplace and ensuring that operations run smoothly. Often, they can be used as tools to implement Kaizen, a Lean manufacturing methodology that eliminates inefficiency and practices change for the better. If you’re looking for ways to jumpstart Kaizen in your workplace, conducting safety checks is a great place to start. Once completed, you can take the results and determine what should be changed in order to eliminate waste, boost operations, and keep workers safe.
Safety Inspections + PDCA Cycle
A major component to practicing Kaizen is the PDCA cycle, a framework that helps improve standards (in this case, safety standards) and carry out positive changes to work processes. This cycle outlines several steps to take in order to achieve continuous improvement. The stages are:
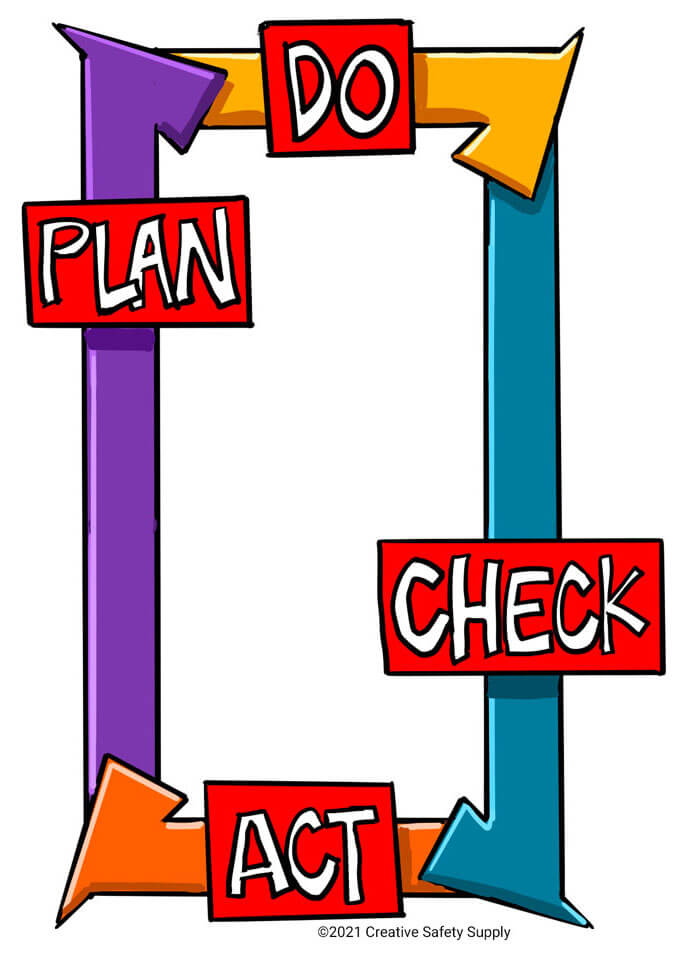
- Plan: Examine the current state of operations and determine whether there are any problems. Develop potential solutions, and a way to carry out these solutions.
- Do: Execute the plans that have been made. All workers involved should understand what changes to make and how to make them.
- Check: Follow up to see how the process of implementing change went, and if it was successful. Determine whether certain goals (such as reducing the risk of injuries) were achieved. Compare the new process to how things were previously.
- Act: If the changes were successful, make them the new standard. If they weren’t, begin back at the “Plan” stage again.
Safety audits and inspections are an important tool to this PDCA cycle. Inspections fall in the “Plan” stage (since they help you assess the workplace for hazards and examine potential safety problems), and audits fall in the “Check” stage (since they are a follow-up to determine how effective changes are, and are used to ensure that the overall safety program is effective).
PDCA is a continuous cycle, and conducting safety audits or inspections is not a one-and-done event. To eliminate hazards and establish a successful health and safety program, you must strive for continuous improvement. Safety audits and inspections, as the foundation to this improvement, will be conducted over and over again. Although they have different areas of focus, together they strive to constantly improve safety in the workplace.
Similar Articles
- Job Hazard Analysis: Addressing Coronavirus Risk in Your Workplace
- Safety Audit
- Quality, Health, Safety, Environment (QHSE) Management Systems
- Understanding Risk Assessments in the Workplace
- Improving Workplace Electrical Safety
- Addressing Biohazard Safety in the Workplace
- Lean Safety | Understanding the Lean 6S Methodology
- Cleaning the Workplace During COVID-19
- Process Safety Management